Laser Displacement Sensors
KEYENCE's laser displacement sensors enable non-contact measurement of a target's height, position, or distance. By pairing multiple sensors, measurements such as thickness and width can also be performed. High-accuracy displacement sensors can be grouped into two categories: confocal and laser triangulation. Both provide accurate, reliable solutions for non-contact measurement, but depending on the application, one type may offer an advantage over the other.
Product Lineup : High Precision Measurement (Reflective Distance Sensors)
The CL-3000 Series confocal displacement sensors are compact 1D laser displacement sensors that use a unique method to ensure high-precision measurement on any material or surface. Using a confocal sensor enables stable measurement on materials ranging from dark rubber to clear films without having to adjust mounting or measurement settings. The sensors are designed with only the lens inside the heads, making them both compact and lightweight, which is ideal for installation in narrow spaces or on robots. All electronics are kept away from the measurement location in the optical unit, providing a stable result that is unaffected by heat or electrical noise. Equipped with features like quad spot processing and optical axis alignment, this series is well suited for a variety of industries and applications, including position or thickness measurement, and it can accurately measure on curved, uneven, or even rough surfaces.
Features
Ultra-Compact Heads for Worry-Free Installation
Ultra-compact and lightweight
The compact sensor heads, including the industry’s smallest at ø8 mm ø0.31”, enable measurement almost anywhere. Utilize previously impossible installation locations, parallel mounting, and other once-unattainable benefits.
Ultra-Compact Design (1/50th the Size of Conventional Models)
Size compared with conventional models: 1/50
-
1Conventional laser displacement sensor
-
2Compact ø8 mm ø0.31" head
New Space-Saving Side View Attachments [CL-V020/V050]
Support for all 4 directions
Compact Head with Best-in-Class Measurement Range*
150 mm ±35 mm 5.91" ±1.38"
* White confocal laser displacement sensor
Advanced Environmental Resistance
Measurement is now possible even at temperatures as high as 200°C 392°F, in ultra-high-vacuum environments, and in explosion-proof areas.
[World's First] Support for Ultra-High-Vacuum Environments*
No organic adhesives
The CL-V020/V050 do not use any organic adhesives in the sensor head, making it possible to minimize outgassing and operate in ultra-high-vacuum environments.
* As a white confocal laser displacement sensor.
First-in-Class 200°C 392°F Heat Resistance
The CL-V020/V050 can handle ambient temperatures of up to 200°C (392°F), allowing for use in environments with drastic temperature fluctuations.
Easy Integration in Explosion-Proof Areas
The dedicated feedthrough (OP-88859) allows for easy integration into hazardous areas without extensive modifications in these locations.
-
1Non-hazardous area
-
2Dedicated feedthrough
-
3Hazardous area
-
4Zone 0/ Division 1
The laser triangulation displacement sensors of the LK-G5000 Series offer high speed and high accuracy for non-contact displacement measurement applications. The sensors utilize advanced hardware such as the RS-CMOS and HDE lens pack to provide reliable results on a range of materials by ensuring the returned light is always in focus. This technology creates a sensor with superior linearity (0.02% of F.S.) and repeatability (0.005 µm). With a max sampling speed of 392 kHz, the LK-G5000 Series can reliably monitor vibrations or catch small changes in fast-moving targets. The head lineup is designed to support a variety of industries and applications, allowing users to select the ideal sensor based on their requirements for measurement range, accuracy, and beam spot size.
Features
Stable Measurement on Any Target
Automatically adjusts the laser light intensity to the optimal level according to real time feedback from the target.
Variety of Sensor Heads Available
Handle any measurement situation thanks to a lineup of more than 20 different sensor heads.
The LK-G3000 Series laser displacement sensors employ high-accuracy Li-CCD and ernostar lensing to provide a flexible solution for measuring displacement. This series offers a broad range of sensor heads to support applications requiring high accuracy or large standoff and has a maximum range of 1 meter (3.3’). The sensors are equipped with a function (ABLE) that automatically adjusts the settings to optimize the reflection from different surfaces, making it possible to measure translucent, rubber, or metal materials stably.
Product Lineup : Reflective Distance Sensors
IX Series image-based laser sensors can measure height anywhere within the area. Camera-based image recognition allows the laser to detect the height of the target point even when workpieces are not perfectly aligned on the production line. The height of where the laser hits the target will vary if the target is tilted or if the target itself is different, but the IX Series can identify the difference in height against the reference. For example, in a parts assembly line, a single IX Series unit can not only check for the presence of parts but also perform seating checks and other height-based inspections. Thanks to its ability to detect height differences, the IX Series is also free from false detections and errors in the presence of glare from glossy surfaces of metal parts or when the detection target point has the same color as the background, offering stable automatic inline differentiation.
Features
Unreliable Detection with Conventional Image-Sensors, but Stable Detection with the IX-H
Conventional Image-Sensors
Low contrast targets result in difficult detection
For targets with similar colors or materials, the difference between light and dark is not always clear, which can result in unstable detection.
IX-H
Target contrast does not matter
Height-based detection ensures stable results even when there is low contrast between the target and background.
Unreliable Detection with Conventional Laser-Sensors, but Stable Detection with the IX-H
Conventional Laser-Sensors
Variations in position and orientation results in incorrect detection
Variations in target position and orientation can cause the spot where the laser hits the target to change, resulting in incorrect detection.
IX-H
Position Adjustment tool tracks misaligned targets
The camera follows the position, orientation, and placement of the target, making it possible to identify the target location for every target.
IL Series CMOS multi-function analog laser sensors are reflective laser displacement sensors that provide the best-in-class detection ability and stability at a reasonable cost. Stable detection is possible without tuning for workpiece types or their surface conditions, so the IL Series can be added to production lines to help make setup, changeover, and product changes easier. With a wide-ranging lineup of sensor heads, including high-accuracy models and long-range (up to 3.5 m 11.5') models, these laser sensors can be applied to diverse applications thanks to their broad dynamic range and environmental resistance. 1 μm repeatability allows for use in high-tolerance detection setups that previous sensors could not stably provide.
KEYENCE's 1D laser displacement sensors enable non-contact measurement of a target's height, position, or distance. By pairing multiple sensors, measurements such as thickness and width can also be performed. High-accuracy displacement sensors can be grouped into two categories: confocal and laser triangulation. Both provide accurate, reliable solutions for non-contact measurement, but depending on the application, one type may offer an advantage over the other.
Descriptions of the various types, measurement principles, and advantages of 1D laser displacement sensors can be found below.
Multi-color Confocal Method
Confocal displacement sensors emit and receive light on the same axis. Multi-color confocal sensors use a light source that emits multiple colors (wavelengths) of light that each have a unique focal distance. The sensor measures the distance to the surface by detecting which color is currently focused on a target. KEYENCE's CL-3000 Series sensors utilize a brighter light source than conventional models, producing stable measurement results throughout the full range, regardless of the surface's reflectivity.
Laser Triangulation Method
Laser triangulation-based displacement sensors utilize the return angle of light reflected from the target to calculate position. Laser light is emitted from the sensor and is reflected off the target surface. Some of that reflected light is focused by a lens onto the receiving element in the sensor head. Depending on the target's distance from the sensor, the return angle of the light will change, striking a different position on the receiver, which can be detected. The LK-G5000 Series employs a high-resolution CMOS to stably measure small changes in displacement.
Confocal Surface Scanning Method
Surface scanning confocal laser displacement meters utilize a tuning fork to rapidly vibrate an objective lens. This moves the focal point of the laser up and down through the measurement range at high speed. The reflected light is focused on a pinhole, where some of the light passes through to the light-receiving element. When the light is focused on the target, more intense light passes through the pinhole, and the objective lens' position is recorded and correlated back to the target position. KEYENCE's LT-9000 Series uses a tuning fork to scan in the z-axis and an oscillating unit to scan in the x-axis, producing high accuracy and stability while employing an ultra-fine beam spot of ø2 µm.
Benefits of Laser Displacement Sensors
One of the major reasons that these sensors can measure targets with diverse materials and characteristics is that they can perform highly precise, non-contact measurements. The optimal laser displacement sensor can be selected to match the application or target material (such as transparent or glossy targets).
If the target is made of metal or some other hard material that does not scratch easily, it can be measured with a caliper, micrometer, or other such instrument that touches the target directly or with an LVDT or other such contact displacement sensor in an inline situation. However, errors may occur due to the measurement pressure when the target is soft. For delicate targets whose quality is affected by contact, such as wafers, thin films, and sensitive hairline metal surfaces, non-contact laser displacement sensors can be used to measure without worrying about errors and target damage. Since they allow for stable, non-contact measurement even of transparent or glossy surfaces, laser displacement sensors enable a wide range of possible applications.
Accurate device positioning is necessary for the automation of processes such as coating, welding, and component mounting. The compact, lightweight head of KEYENCE’s multi-color confocal method laser displacement sensor can be easily installed on devices and accurately determines the distance to the target, allowing for highly precise position control without sacrificing device operation.
Separating the spectroscope unit and leaving the lens as the only key part in the head has given the CL-3000 confocal displacement sensor a compact and lightweight head that can be installed easily in machines. Measurement is performed with light along the same axis, so the heights of narrow gaps in targets can also be measured with no blind spots. Furthermore, the head generates no errors due to heat or electrical/magnetic noise, ensuring stable measurement. For device control, laser displacement sensors can measure target height at high speeds, feeding back this information to control devices. This allows for heights of stepped targets or targets that are slightly tilted during conveyance to be measured in real-time. The result is that quality can be maintained in automatic processes.
Laser Displacement Sensor Case Studies
Thickness measurement of glass (patterned on one side)
When the surface reflectance differs between the glass surface and the pattern surface, tracking errors traditionally occur at the pattern surface when the thickness is measured with laser displacement sensors positioned on each side of the glass. The CL-3000 confocal displacement sensor uses a multi-color confocal method that measures the position where the projected light is in focus, allowing for stable and highly precise measurement unaffected by differences in the intensity of the light reflected from the target. This minimizes the effect of tracking errors, improving the inspection cycle time.
Dispenser nozzle height measurement and control
Ensuring advanced, high-accuracy, automatic coating requires not only a sophisticated dispenser robot but also a high-performance displacement sensor that moves together with the nozzle, working as the eye of the dispenser. Installing the CL-3000 Series confocal displacement sensor so that it follows the dispenser nozzle enables nozzle height control through real-time measurement and feedback of the target height. The compact and lightweight head can be installed easily next to the dispenser nozzle and reduces residual vibration when the operation stops. The multi-color confocal technology uses a coaxial system to provide a wider measurement range and ensures stable height measurement and feedback control without being affected by the transparent, mirror, or glossy surfaces of materials or by shapes such as concaves, differences in height, and inclined or rounded surfaces.
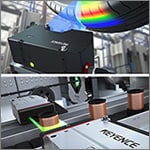
The Measurement Library is a website that provides thorough explanations of measurement basics, measurement system selection, application solutions, the types and principles of measurement with laser displacement sensors, and case studies where problems are solved through the installation of such sensors.
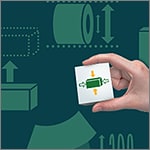
The Selecting a Measurement Sensor site introduces proven solutions in various industries, including automotive, film & sheet, and electric & electronic components for laser profilers, as well as our other laser displacement sensors and measurement systems. Applications can also be explored by measurement types, such as thickness, width, height, height difference, and 3D inspections.
Frequently Asked Questions About Laser Displacement Sensors
CL-3000 Series confocal displacement sensors can stably measure not only transparent glass but also a wide variety of target materials and shapes with high precision. Of course, the non-contact measurement eliminates the concern of damaging the glass. With the CL-3000 Series, up to six heads can be connected simultaneously to a single controller. For example, the glass's flatness can be checked stably by measuring the four sides and the center of the glass with a system consisting of one controller and five heads or by measuring six ends with four to six heads. Furthermore, as discussed above, all sensors are compact and lightweight, making them suitable for mounting in narrow spaces or robotic arms. The electronics are kept away from the measurement location in the optical unit, thus providing a stable result that’s unaffected by both heat and electromagnetic noise.
Generally, diffuse reflections occur due to the laser light penetrating the inside of the PCB or its solder mask, which is a lacquer-type material that usually comes in several different colors. The semi-transparent nature of the solder mask paired with different colors could potentially cause diffuse reflections when it is measured with a laser displacement sensor. This may lead to unstable measured values. KEYENCE CL-3000 Series confocal displacement sensors can emit laser light at multiple wavelengths to calculate and measure just the wavelength band of the light that brought the surface of the target into focus. Stable measured values can be obtained with high precision even for PCBs and other such targets easily penetrated by light—glass, silicon wafers, micro lenses, etc. The advantage of this technology is that it can even enable you to measure the surface displacement of a soap bubble without physically affecting the surface.
The purpose of a distance displacement sensor is to measure the amount of movement or displacement of an object concerning the reference point. Thanks to their design, these sensors usually measure displacements in the micron and even nanometer range, with some models being capable of measuring finer than the nanometer range. The purpose of these sensors, at least in the manufacturing sense, is to provide precise measurement of position—a feature that has many applications.
Measuring position can tell us about the object’s movement. For instance, it can be used to monitor machinery operating within a certain range and for quality control. The latter is perhaps the most interesting, as it’s associated with metrology, allowing us to check the product’s exact measurement specifications by measuring displacement.
Several factors play a crucial role in determining the adequate sensor for your application, ensuring the device and its measurement method suit your specific need. Range, resolution, and accuracy are, by far, the most important factors when selecting your displacement measurements.
However, as seen above, not all measurement methods suit all materials, and some sensors are better at scanning certain materials over others. You should also consider sampling speed, especially if you’re measuring dynamic displacement—in which case you’d want a sensor with an adequate sampling speed.
Though they’re both non-contact laser displacement sensors, confocal and laser triangulation sensors operate on fundamentally different principles, which makes them suitable for different applications. Laser triangulation relies on emitting the light onto a surface and measuring the light the surface reflects onto the receiving element. Any changes in the angle of reflected light are proportional to the displacement in the target surface.
Confocal sensors, on the other hand, transmits a variety of wavelengths of lights and looks at which wavelength is in focus on the target surface. As the focused wavelength changes, we can determine the change in the position of the target. However, thanks to their design, which includes a series of optical lenses housed inside a cylindrical tube, confocal sensors tend to be more stable compared to laser triangulation sensors. However they also tend to be slower, giving the edge for high-speed applications to laser triangulation sensors.
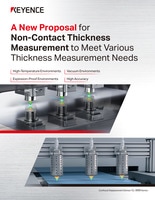
Thoroughly explains the measurement principle as well as how the functions and performance of the CL-3000 Series confocal displacement sensors solve problems with conventional thickness measurement. If you are concerned about thickness measurement, this is the only guide you need.
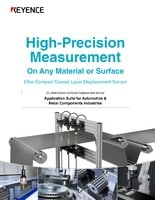
The ultra-compact head of the CL-3000 Series confocal displacement sensors enables high-precision measurement on any material or surface. Diverse applications using this characteristic in the automotive and metal components industries are contained in this guide.
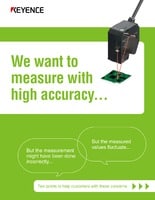
Depending on setup conditions, laser displacement sensors may not achieve the accuracy listed in the specifications. Using laser displacement sensors that employ general triangulation as an example, this guide explains the causes of measurement errors, and methods to eliminate errors and increase stability.
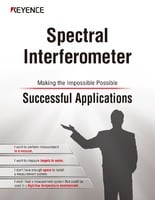
KEYENCE’s SI Series of spectral interference displacement sensors has been used to solve various problems in a wide variety of industries including semiconductors, glass, film, and automobiles. This guide contains various applications resulting in successful improvements.
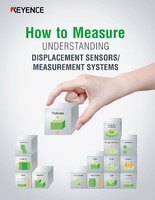
This guide contains a wide range of measurement methods: thickness, width, height/step, outer diameter, stroke, run-out/vibration, eccentricity, warpage/flatness, angle, gap/clearance, target meandering, radius, inner diameter, positioning, profile, and 3D shape.