KEYENCE’s Sustainability
Solving Social Issues Using Our Products
Improving Productivity
Against a backdrop of labor shortages and other social issues, manufacturers are pursuing automation and streamlining as a means to increase productivity. KEYENCE is helping to reduce production time and improve throughput by proposing products and applications that lead to improved manufacturing efficiency.
The optical-axis alignment function allows for easy installation.
Enhancing Quality
As the sophistication and miniaturization of products increase thanks to technological innovation, advancements in manufacturing must keep pace. Consumers demand ever higher quality year after year, and a defective product can severely harm a company’s brand image and reduce profitability. KEYENCE helps solve the problems these advanced manufacturing sites must grapple with.
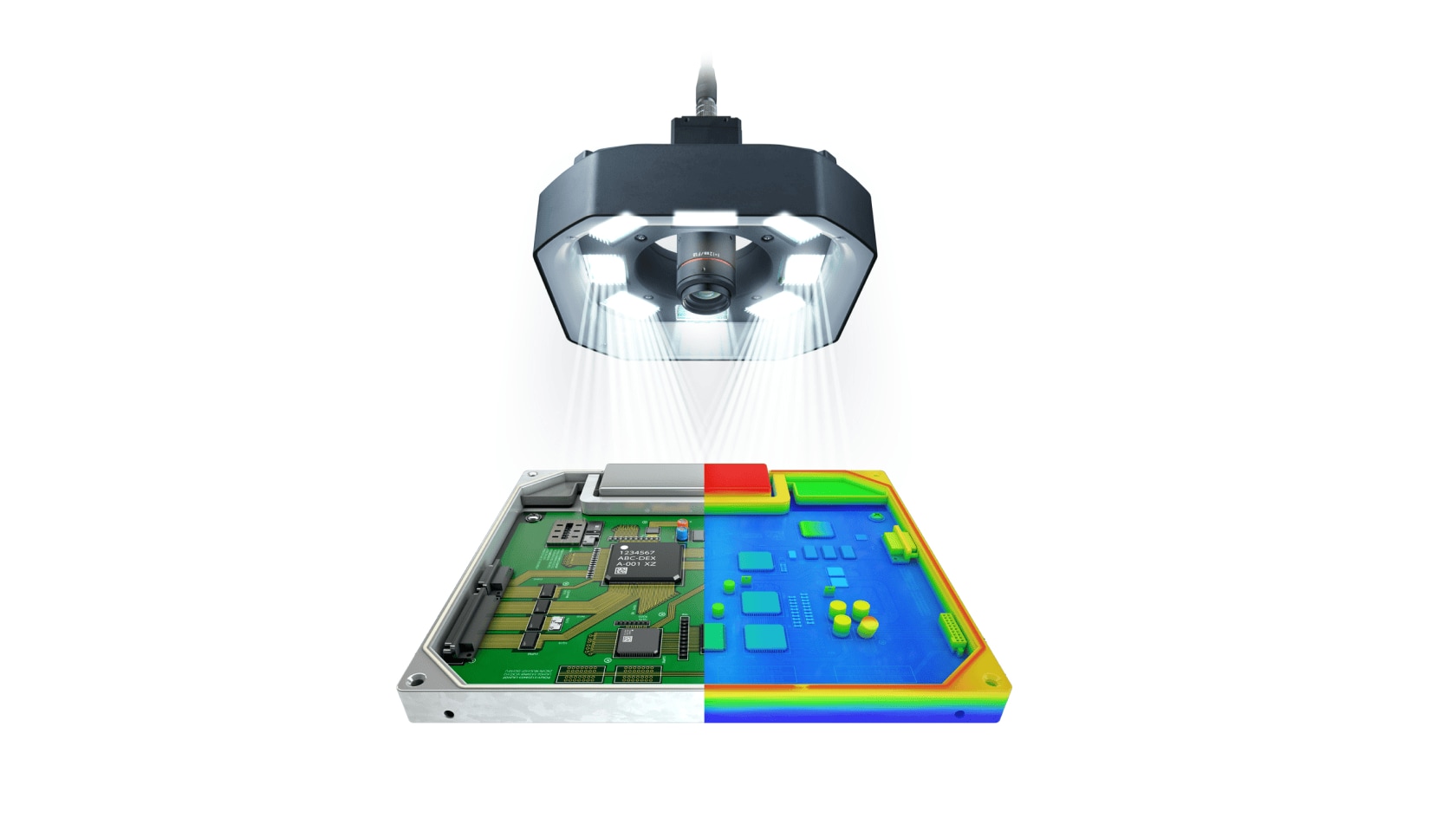
Ensuring Safety in the Workplace
KEYENCE creates products that help ensure safety at manufacturing sites. Specifically, we are promoting the improvement of on-site safety by developing safety equipment that ensures that workers are safe from hazardous elements such as machinery and robots while maintaining a high level of productivity.
SZ Series Safety Laser Scanner
GL Series Safety Light Curtain
GS Series Safety Interlock Switches
Improving the Working Environment
Safety measures are required in Japan when handling ink and solvents that use organic solvents and alcohols. A risk assessment must be performed to check the harmfulness of ink and solvents when using an industrial inkjet printer. KEYENCE inkjet printers are equipped with various features to prevent health risks.
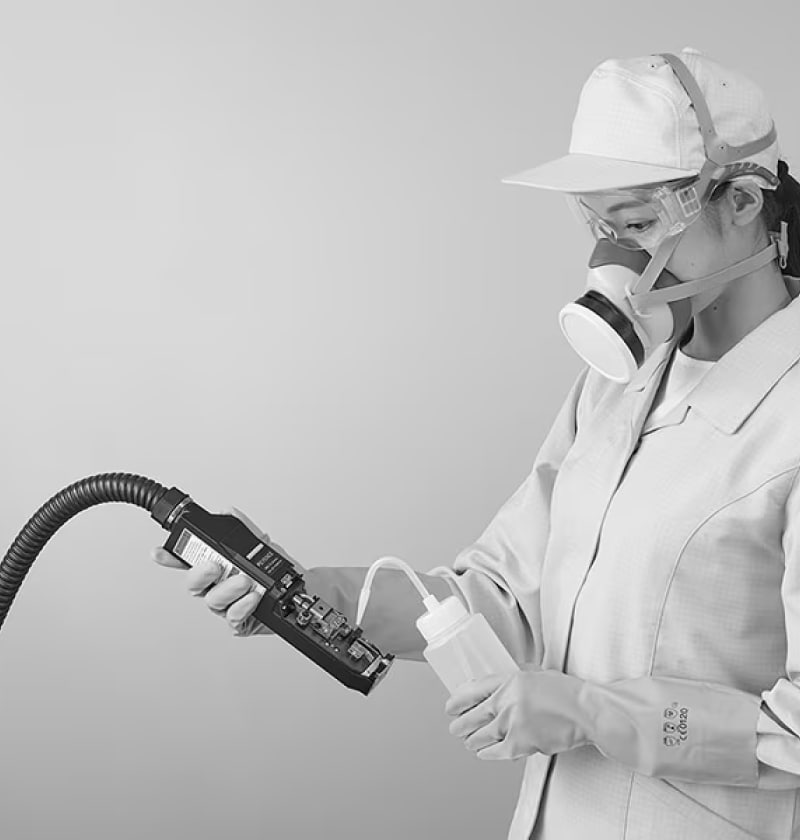
In the past, separate equipment was required to safely perform maintenance.
Daily maintenance is required to use an inkjet printer. Businesses must research these measures based on the results of the risk assessment.
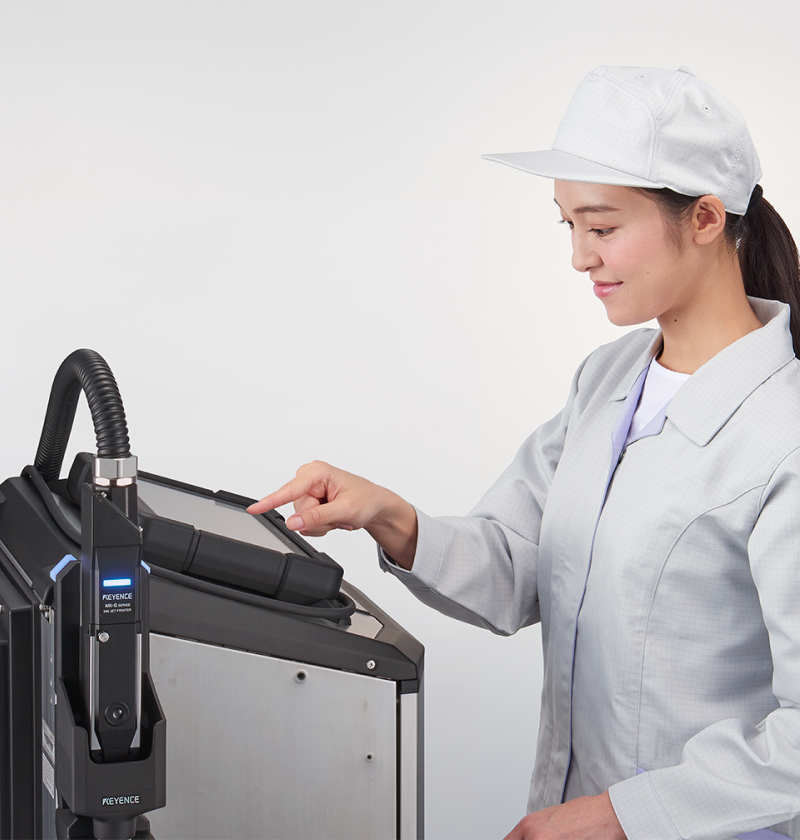
Anyone can perform maintenance of the MK-G Series safely.
The MK-G Series has a new design to prevent exposure to and inhalation of ink and solvent. No special measures or additional cost is required unlike with conventional inkjet printers.
- * Not including special work to replace the pump. The worker must determine the measures to take according to the work details.
Helping Reduce Energy and Resource Consumption in Factories
Environmental issues such as climate change are an urgent problem on a global scale, and year after year the need for measures to conserve energy and resources in factories is growing. KEYENCE, through our products, supports our customers’ initiatives to conserve energy and resources.
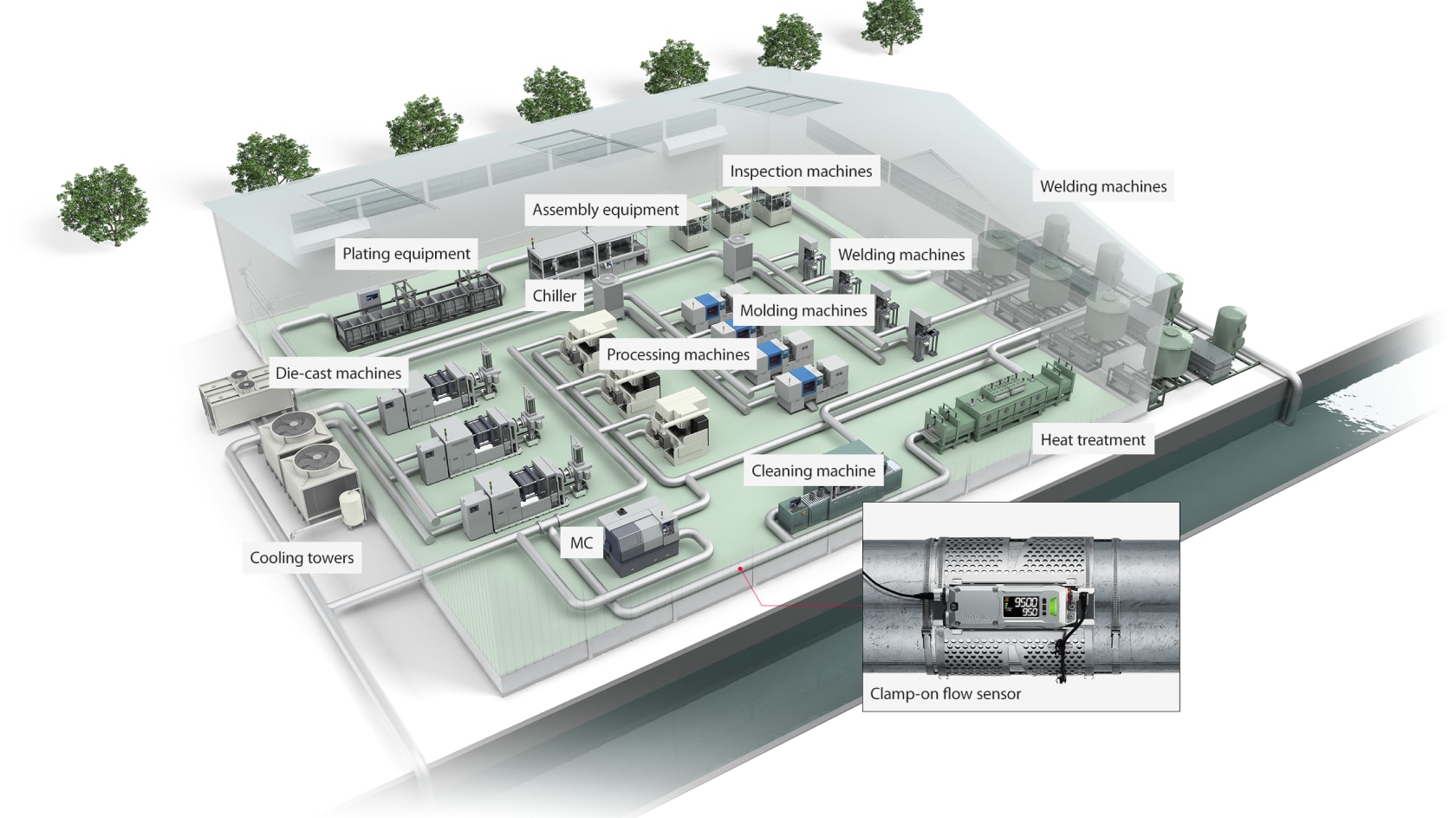
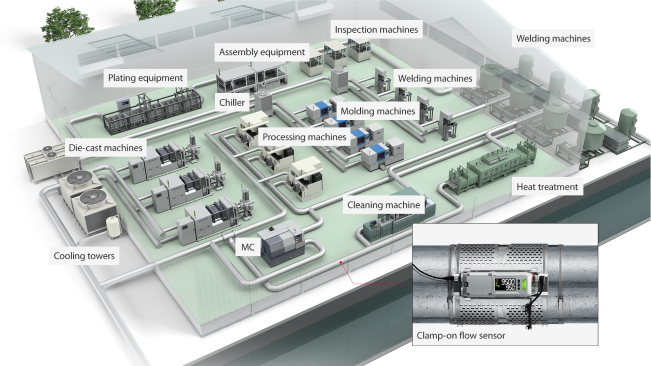
Reducing Environmental Impact at Customer Locations
Reducing Environmental Impact at Customer Locations
Various liquids and gases—including cutting water, cutting oil, coolant, hydraulic oil, argon gas for welding, air for air blow, and paint for coating—are used during production at factories. These fluids are conveyed through facilities using pumps, fans, and other equipment. The pumps, fans, and compressors that move these fluids use large amounts of electricity while running. Flow sensors play an important role in energy conservation by managing and recording the usage of fluids, so wasteful conveyance is kept to a minimum.
Clamp-on flow sensors that can be installed on existing pipes
-
Clamp-on flow sensor for liquids
-
Clamp-on flow sensor for gases
Saving Energy with Flow Sensors
In factories, compressed air is used for air tools, presses, spray guns, and air cylinders that power robots and machine tools. Compressors are used to produce this compressed air,
which consume a large amount of electricity. These compressors, which are so important to the operation of factories, tend to leak large amounts of air, which is a major source of
losses. Accurately managing the flow of compressed air is very important to prevent losses and save energy. Doing this allows for optimization of the amount of electricity used by
the compressor, leading to reduced energy consumption.
Flow sensors allow for monitoring and visualization of the flow of compressed air. This means that air leaks can be detected, making them a highly effective and important part of
energy-saving measures, such as lowering the pressure according to usage, using an inverter, or limiting the number of units.
Usage example: Managing use of compressed air
By determining the flow rate from the receiver tank, the amount of compressed air used throughout the factory can be measured.
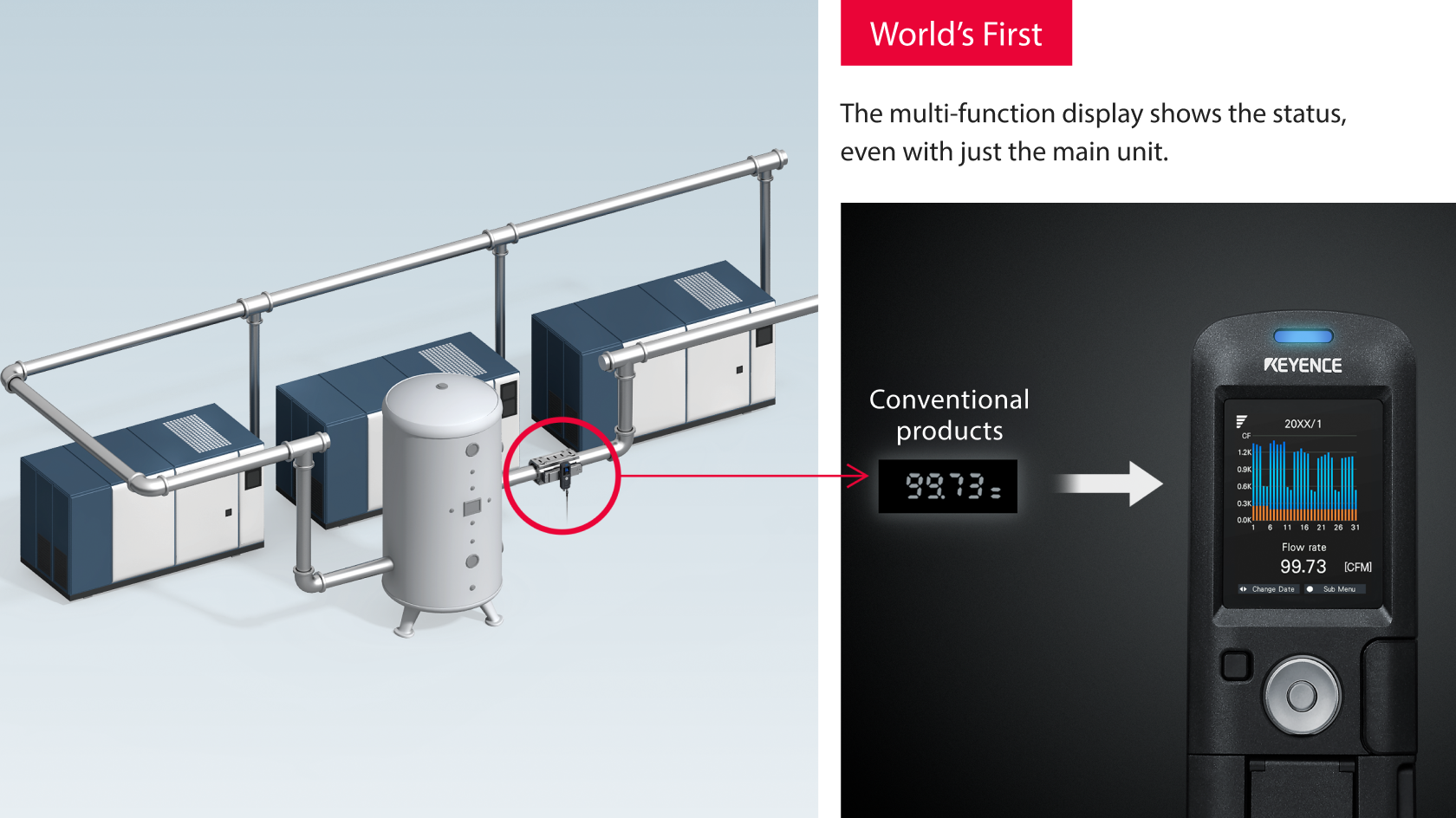
Saving Energy with Pressure Sensors
Many machine tools use hydraulic cylinders and hydraulic valves. Oil is used not just to run machines, but also for cleaning and cooling. Conventional tools frequently suffer from insufficient hydraulic management of these processes. When considering energy conservation, it is very important to manage hydraulic pressure and keep unnecessary pressure application to a minimum. The most effective way to accomplish hydraulic management is by using oil pressure sensors. By managing oil pressure at all times, changes can be monitored, and deterioration and leaks of hydraulic oil can be detected easily.
-
Hydraulic management of machine tools
-
Energy-Saving Measures Based on Visualization of Management Values
To implement energy-saving measures in the manufacturing industry, data must be acquired with devices like flow and pressure sensors, which can then be used to visualize how much energy is being used, where it is used, and in what process. The PDCA (Plan-Do-Check-Act) cycle is used to study energy-saving measures based on an understanding of energy use, and to repeat the process of implementation and improvement to continuously improve practical energy-saving measures.
A touch panel recorder that can be connected to a machine tool hydraulic control PC, PLC, or data server
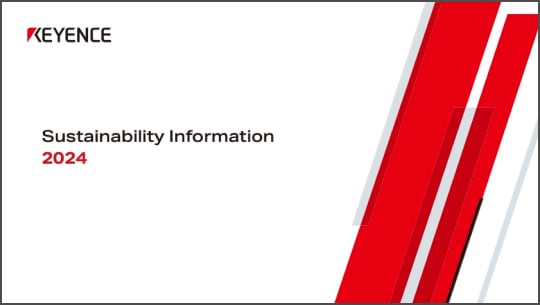