Continuous Inkjet Printers / Case Coder
Continuous Inkjet Printer Working Principle Guide
Continuous Inkjet Printers (CIJs) are industrial inkjet printers that rely on a constant flow of ink from a pressurized source. The continuous inkjet printer working principle has the ink continuously fed to the print head and directed at the substrate, with the unused ink recirculated back into the printer system.
KEYENCE’s CIJ printers, primarily the MK-G Series, consist of two main parts: the controller unit and the print head. Inside the controller, the pump pulls the printing ink from the main tank, which contains the mixture of ink and solvent.
The pump pressurizes the ink pulled from the main tank and feeds it into the cannon in the print head. Then, a crystal or piezoelectric oscillator vibrates in this cannon, pushing out a stream of droplets through the nozzle.
A charging electrode plate then imparts a variable negative electrostatic charge on the droplets used to print. Ink droplets then pass between two electrically charged plates, also known as deflecting electrodes. Deflecting electrodes are charged with 7,000 volts and generate a strong electric field that deflects the negatively charged ink droplets.
Circulation path
-
1Main tank
-
2Pump
-
3Pressure-reducing valve
-
4Piezoelectric element
-
5Nozzle
-
6Electrostatic electrode plates
-
7Electrostatic sensor
-
8Deflecting electrode plates
-
9Gutter
-
10Pump
The bending force acts on the ink particles according to the level of their charge to change their trajectory—the direction in which they travel. Simultaneously, the target substrate, or the print head, is moved perpendicularly to the travel direction of the ink droplet to print the desired content. In short, the variable voltage droplets create the Y height of the text, while the lateral or X movement of the substrate creates the width of the text.
The ink droplets not used for printing aren’t electrostatically charged or deflected by the electrodes toward the substrate. Instead, they’re collected in a pipe called the gutter, where they’re pulled by the recirculation pump, filtered, and pushed back into the main tank, where it’s reused for printing.
Printing Principle
- Step 1: Pressurized ink is supplied to the print head from the controller.
- Step 2: Ink is fed to the nozzle which has the piezoelectric oscillator and discharge hole.
- Step 3: The ink is discharged while being oscillated by the piezoelectric oscillator, and it is simultaneously given a negative electrostatic charge. The ink is formed into an ink column, but when saturated with the negative charge, the ink becomes particles, and those particles separate from the ink column.
- Step 4: The electrostatic detection sensor monitors the ink particles to ensure they receive the appropriate electrostatic charge. This prevents malfunction.
- Step 5: The ink particles that fly from the nozzle pass between two deflecting electrodes where an electrical field is generated by a voltage of around 7000 V. At this time, a bending force acts on the ink particles according to their electrostatic charge to change the direction they fly in. Together with this, the target or print head is moved in the vertical direction to print by creating the shapes of text and numbers.
- Step 6: Ink not used for printing is collected in a pipe called the gutter and reused.
We’re here to provide you with more details.
Reach out today!
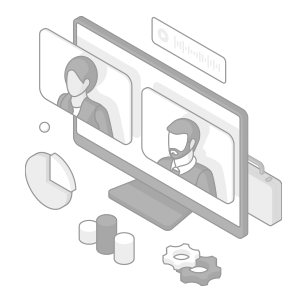
Importance of Understanding the Inkjet Printer Working Principle
In the past, there were several reasons why understanding continuous inkjet printer working principles was critical, especially in the industrial setting. The primary reason is print quality and uptime optimization: knowing how inkjet printers operate allows you to optimize the print setting for the best possible print quality and production time.
However, there’s also a matter of maintenance. Knowledge of the inkjet printer's working principle and mechanism can help with diagnostics, troubleshooting, and maintenance and fix some common problems, such as clogged nozzles, dirty print heads, and poor quality/fuzzy print.
Fortunately, KEYENCE's MK-G Series printers remove the need to understand the working principles of CIJ. Anyone can clean, maintain, troubleshoot, and even replace parts with ease. No specialized training or service technicians are required. Much of this is possible because of the MK-G Series smart dock, which acts as a diagnostic tool and then completes the appropriate cleaning or troubleshooting at the push of a button. If anything does require maintenance, step-by-step video walkthroughs allow part replacements to be completed with no tools.
Self-diagnosis and optimal cleaning with the MK Dock
When the print head is placed in the MK Dock, the unit will perform self-diagnosis to check for faults and automatically resolve the issues. A bright LED enables users to see the printer status even from far away.
Using the MK Dock enables self-diagnosis and cleaning to ensure stable startup
The requirement of understanding the working principle of the inkjet printer was so crucial for those in the industry using other conventional continuous inkjet printers prior to the MK-G Series. Trained maintenance staff were needed to constantly upkeep conventional continuous inkjet printers with reactive maintenance. The MK-G Series can proactively reduce the need to constantly clean and adjust print head settings.
A clear understanding of how an inkjet printer works can also aid in understanding why KEYENCE designed the MK-G Series with all of the factors in mind to be a better option for high-volume industrial inkjet coding applications.
Are you looking to enhance your print quality and streamline maintenance for your industrial printing requirements? Explore the cutting-edge technology of KEYENCE's MK-G Series continuous inkjet printers.
Get in touch with us today!
Get detailed information on our products by downloading our catalog.
View Catalog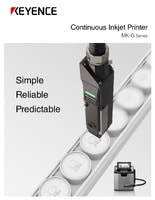
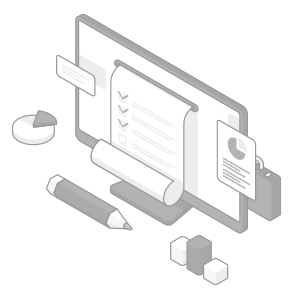
Related Downloads
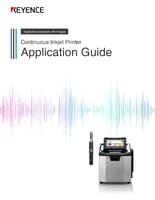
This guide explains continuous inkjet (CIJ) printer applications together with pictures and illustrations. It contains many installation examples in various industries divided into food, medicine, and cosmetics; electrical machinery and electronics; and automotive, metal, and others. These examples show printing on targets specific to each industry.