Positioning Sensors
These easy-to-use sensors can be used in a large variety of diverse applications such as highly accurate positioning and product type difference checking. The lineup also includes a brand-new image-based laser sensor that automatically corrects target misalignment to simultaneously detect multiple points with high accuracy.
Product Lineup : Reflective Laser Sensors
IX Series image-based laser sensors can measure height anywhere within the area. Camera-based image recognition allows the laser to detect the height of the target point even when workpieces are not perfectly aligned on the production line. The height of where the laser hits the target will vary if the target is tilted or if the target itself is different, but the IX Series can identify the difference in height against the reference. For example, in a parts assembly line, a single IX Series unit can not only check for the presence of parts but also perform seating checks and other height-based inspections. Thanks to its ability to detect height differences, the IX Series is also free from false detections and errors in the presence of glare from glossy surfaces of metal parts or when the detection target point has the same color as the background, offering stable automatic inline differentiation.
Features
Unreliable Detection with Conventional Image-Sensors, but Stable Detection with the IX-H
Conventional Image-Sensors
Low contrast targets result in difficult detection
For targets with similar colors or materials, the difference between light and dark is not always clear, which can result in unstable detection.
IX-H
Target contrast does not matter
Height-based detection ensures stable results even when there is low contrast between the target and background.
Unreliable Detection with Conventional Laser-Sensors, but Stable Detection with the IX-H
Conventional Laser-Sensors
Variations in position and orientation results in incorrect detection
Variations in target position and orientation can cause the spot where the laser hits the target to change, resulting in incorrect detection.
IX-H
Position Adjustment tool tracks misaligned targets
The camera follows the position, orientation, and placement of the target, making it possible to identify the target location for every target.
IL Series CMOS multi-function analog laser sensors are reflective laser displacement sensors that provide the best-in-class detection ability and stability at a reasonable cost. Stable detection is possible without tuning for workpiece types or their surface conditions, so the IL Series can be added to production lines to help make setup, changeover, and product changes easier. With a wide-ranging lineup of sensor heads, including high-accuracy models and long-range (up to 3.5 m 11.5') models, these laser sensors can be applied to diverse applications thanks to their broad dynamic range and environmental resistance. 1 μm repeatability allows for use in high-tolerance detection setups that previous sensors could not stably provide.
Rugged, Reliable, Repeatable Laser Measurement Simplified. KEYENCE brings you an economical analog laser sensor
Product Lineup : LVDT / Contact Sensors
To increase longevity—a common challenge with contact-type displacement sensors—the structure of the main body has been fundamentally re-examined for the High-Accuracy Digital Contact Sensor GT2 Series. The structure, including the relay connector and cable, ensure stable measurement even in environments with splashing water or oil. In addition, the reduced weight of the spindle means minimal friction wear and significantly improved durability. A wide variety of sensor heads are available, including pencil type, air push-type, and low-stress type. The GT2 Series offers two types of detection methods: LVDT (linear variable differential transformer) and Scale Shot System II. This allows use across various applications. The varied lineup of communication units enables communication with PCs and PLCs from various manufacturers.
Features
Choose from 29 Different Head Variations
The GT2 Series is available in a wide range of heads, including pencil, air, and low-speed pressure types. Choose a design most suitable for the application.
Select from a Variety of Communication Methods for Easy Integration
With an increased focus on traceability and IoT, the need to record values is becoming ever more pressing. KEYENCE sensors include a varied lineup of communication units capable of communicating with PCs and PLCs from various manufacturers. Simplified amplifier wiring makes it possible to greatly reduce wiring work.
The General Purpose Digital Contact Sensor GT Series is a contact type sensor designed for ease of use and reliability. It can be installed easily in existing facilities, allowing for quick startup of the production line after installation. It also has an easy-to-see display and a self-diagnostic function for checking for conditions such as a trapped spindle or cable disconnection. There are two types of mounting for the amplifier: DIN type for rail mounting and panel type for panel mounting. Selecting the correct type for the installation environment is effective for simplified wiring. Various functions are included to complete the setting with minimum steps. The sensor can be used immediately after installation. The easy-to-see indicators clearly show judgment results and errors during measurement.
Product Lineup : Thrubeam Laser Sensors
IG Series multi-purpose CCD laser micrometers provide high-precision differentiation that is unaffected by how much light the target transmits. This series uses a line-charge coupled device (L-CCD) as its light-receiving element. Instead of using received light intensity, it captures the edge of transmitted laser light, so it can perform high-accuracy, stable differentiation with 5 μm repeatability and ±0.1% linearity. This makes the IG Series capable of supporting various applications, including edge detection and positioning of clear glass, precise recognition of workpiece OD, feedback control while detecting a sheet edge, and roll gap measurement. The positioning monitor on the main unit facilitates optical-axis alignment when starting up a line and during changeovers.
Features
Easy To Use
The position monitor makes it easier to align the optical axis. Easily perform optical axis alignment by adjusting the sensor head so that all of the position monitor lights turn red.
Environmental Resistance
The enclosure satisfies the IP67 rating based on the IEC standards and remains watertight even after being held at a depth of one meter for 30 minutes. The enclosure is resistant to adverse environments and offers long-term durability.
IB Series thrubeam-type laser detection sensors cater to a diverse range of applications by differentiating received light intensity with high accuracy. This series uses a photodiode (PD) for its light-receiving element. By accurately detecting the changes in received light intensity, it can support various applications without being affected by the target. For example, the IB Series can be used for applications that are impossible with photoelectric sensors, such as the detection of liquid crystal glass and liquid turbidity, differentiation of film types, tilt detection of chips, and incorrect seating of caps, all at low cost. The compact sensor head is equipped with an alignment LED, so optical-axis alignment is easy.
Product Lineup : Ultrasonic Sensors
FW Series high power digital ultrasonic sensors are super multi-reflective, non-contact level switches that can perform stable detection of any target. They are not affected by the color, pattern, luster, or transparency of surfaces, so they can be used for any target, including liquid levels, metal, and glass. The IP67-compliant sensor heads have excellent environmental resistance and emit powerful ultrasonic waves that penetrate some dust and dirt to detect workpieces. The newly included A.W.S. (active wave stabilizer) algorithm eliminates the influence of target vibration or ambient light. The N.O.D. (nearest object detection) function detects only the nearest target without being affected by the luster or shapes in the background. This makes it possible to perform stable detection of any target in any installation environment.
Features
Can Be Used for All Types of Targets
The FW Series easily detects metal, glass, liquid level or other targets that have been difficult to detect with reflective-type photoelectric sensors. Also, the detections are not influenced by the color, pattern, or luster of the target surface.
High Stability and Reliability
A new algorithm A.W.S. (Active Wave Stabilizer)* stabilizes detection while avoiding the influence of target vibration or external disturbances.
Positioning sensors identify positions by detecting the target’s distance, height, width, and other information. Different sensors can be selected according to the workpiece shape, conditions, and application.
Contact-type displacement sensors that operate on the typical principle of linear variable differential transformers (LVDT) detect and measure the changes in the height of the target by capturing the mechanical linear movement of the probe as displacement. For non-contact displacement sensors, laser displacement sensors are the most common among optical types due to the linearity of the light. Laser displacement sensors can be further classified into reflective and thrubeam models. Reflective models detect the position and height based on the distance from the target. Thrubeam laser displacement sensors can continuously detect not only the position of objects passing vertically through the band of signal light, but also their outer and inner diameters.
Types and working principle of positioning sensors
Sensors used for positioning workpieces can be selectively applied according to the workpiece shape and detection conditions. Detection methods are broadly categorized into two groups: contact and non-contact. Contact displacement sensors (touch sensors) that bring a probe into direct contact with a target are typical contact-type positioning sensor. Laser displacement sensors are a typical example of non-contact positioning sensors, using the linearity of laser light for detection. The following section explains the types and working principles of these typical positioning sensors.
Contact-type positioning sensors
Linear variable differential transformer (LVDT) method:
An LVDT displacement sensor detects mechanical linear movement as displacement and converts it to an electrical signal.
This type of sensor has a core at its center with coils located around it. A probe is attached to the tip of the core to make up a spindle. The spindle is pushed against the target with a spring mechanism, sliding along with the changes in the target’s height. A magnetic field is generated when current passes through the coil, moving the core inside. The resistance of the coil and the output signal level change according to the amount of core movement. The movement of the core shows changes in the shape of the target, which means displacement can be measured from the changes in the output signal level. These changes can be used for height measurement and positioning.
Scale (pulse count) method:
Contact displacement sensors using the scale method are also called pulse-count sensors.
The vertical movement of the spindle caused by it coming into contact with the target is converted by an internal scale into signals to detect the position. Pulse counting comes in two types: magnetic pulse counting, which counts pulses using an S(N)-pole magnetic field; and optical pulse counting, which counts pulses using a light receiving element with slits on the scale as a light source.
The detection accuracy of the scale method depends on the accuracy of the built-in scale.
KEYENCE developed the Scale Shot System II, the world’s first system that uses a CMOS sensor for high-speed scanning of an absolute value glass scale that incorporates slits with complex patterns that vary depending on the position. This allows the sensor to measure height (position) with precision, obtain the absolute position, and detect position information, which means it does not need zero point adjustment. These properties also offer other advantages, such as protection against tracking errors and good temperature characteristics.
However, contact-type positioning sensors are not suitable for use with soft workpieces that can be deformed by the probe and workpieces that are prone to scratching.
Non-contact positioning sensors
Reflective laser displacement sensors:
One sensor head emits laser light on the target, and the reflected light is received by the built-in light receiving element (e.g. CMOS). This type of sensor can capture the distance to the target based on the changes in the position of the reflected light received by the CMOS through the receiver lens and detect the position and height. This principle is called the triangulation method because the laser’s path is a triangle.
Laser displacement sensors that use a CMOS as the light receiving element can provide high-accuracy position detection.
Thrubeam laser displacement sensors:
This type of sensor creates a band of laser signal light between the laser transmitter and the receiver. When a target passes through the signal light, part of the signal light is blocked. The changes in the amount and position of laser light coming through are captured by the light receiving element (e.g. CCD) to detect the target without coming into contact with it.
The width of the band of the laser varies, which allows use in a variety of applications, such as target position and edge detection as well as clearance and inner/outer diameter measurement, regardless of the workpiece shape or purpose.
Laser displacement sensors can not only position targets without touching them, but also support a wide range of applications by placing multiple sensor heads according to the workpiece shape or purpose. Multiple reflective models can be placed targeting flat workpieces from different directions to measure their flatness based on height differences. Thrubeam models can detect the outer and inner diameters of objects.
Benefits of Positioning Sensors
Compared to other positioning sensors, laser displacement sensors can detect and differentiate targets of any material due to their non-contact operation. Their flexibility in installation also means that they support a variety of applications, including positioning a diverse range of workpiece shapes and sizes as well as detecting heights and outer/inner diameters.
Laser displacement sensors are generally unaffected by the target’s surface conditions, allowing their use with various workpieces. Another notable advantage is their freedom of installation. Thanks to the linearity of laser light, these sensors can be flexibly installed without concerns about detecting distance. Also, laser light does not diffuse, so these sensors can target narrow clearances while preventing scattered light effects. Environment-resistant sensor heads can withstand use in high-temperature conditions while high-power type thrubeam laser displacement sensors have much lower false detection rates even in the presence of some dust.
Compared to other positioning sensors, laser displacement sensors can continuously detect and differentiate positions without stopping the targets. Therefore, they do not compromise the cycle time of production lines or scratch surfaces or otherwise damage workpieces thanks to their non-contact detection.
Unlike vision sensors, laser displacement sensors do not need shutter releases, and therefore they can continuously detect the edges of moving workpieces. Thrubeam models can continuously detect the outer diameter of extruded bar-shaped workpieces or the entire length of an edge of a sheet or film on a roller machine. Other possible applications include run-out detection. As both reflective and thrubeam types do not need to come into contact with targets, they can detect soft-material workpieces without affecting their shapes. They are also effective for use with delicate, easily-scratched targets.
Some sensor heads for positioning sensors provide micron-order beam spots, which enable detection of tiny areas on small workpieces. Sensors using a red light laser can be easily installed by looking at the beam spot while adjusting the detection position.
Compared to other positioning sensors, laser displacement sensors can accurately detect tiny areas on small targets (for example, approximately 200 × 750 μm at the reference distance for the IL-030), which is difficult with contact-type displacement sensors. Because laser light has better linearity compared to LEDs, these sensors are capable of accurately detecting deep, narrow areas from a distance. This allows laser displacement sensors to help significantly reduce installation time and effort compared to photoelectric sensors. A laser displacement sensor with red laser light can be useful when checking whether the beam is hitting the intended spot.
Positioning Sensor Case Studies
Incorrect bolt or screw height detection
Laser displacement sensors with a built-in camera are useful when inspecting the seating and height of automotive parts. IX Series image-based laser sensors can simultaneously measure up to 16 points within their 108.5 × 81 mm (4.27" × 3.19") field of view. The camera identifies the targets through imaging and follows multiple specified points, and the laser detects the individual heights of those points and height differences. A single IX Series unit can achieve what previously required multiple sensor heads, reducing the necessary installation space to a minimum. Misaligned workpieces in a transfer line can be automatically corrected to the proper position in images as long as they are within the scan area, so strict positioning is no longer necessary.
Edge position detection during film transfer
Workpieces meandering during transfer is a cause of wrinkles and slacks in films and other thin products. Continuing to wind the workpiece with the edge position misaligned can cause slacks due to uneven roll winding, resulting in the workpiece meandering. This produces defective rolls and reduces yield. IG Series multi-purpose CCD laser micrometers provide continuous, high-precision differentiation of the edge positions of workpieces in motion. The newly developed optical system enables stable edge detection and monitoring of thin, transparent, and meshed films and sheets. The detected film transfer status is also provided to the system as feedback, which allows for edge control.
Measurement and differentiation of product dimensions and outer diameter
If you want to prevent workpieces sustaining scratches or other damage from contact-type measuring instruments, you should consider non-contact measurement using a vision system. However, if your purpose of measurement is limited to the workpieces’ thickness, width, height, and/or warpage, a vision system is too costly to introduce and too complicated to operate considering the application. IL Series CMOS multi-function analog laser sensors can detect targets of any color or material at reasonable cost. By measuring displacement at multiple points, the IL Series can detect workpiece shape and warpage as well as measure the thickness and width of extruded products.
Depending on type, positioning sensors have different precautions and necessary actions when installing and using them. The following section explains the key points for installing and using each common type of positioning sensor.
Contact-type displacement sensors
Contact-type displacement sensors touch targets directly with a probe to detect their positions by calculating the changes in the spindle height. To ensure that a contact-type displacement sensor stably detects targets inline, you must take the following precautions during installation and use.
During installation
The sensor must be installed with the correct angle in relation to the direction of position detection, and this angle must be maintained. In general, contact-type displacement sensors have a small measurement point. This means that once the angle in relation to the direction of detection shifts, the angle of probe contact shifts as well, which may result in errors.
Maintaining accuracy and stability
While contact-type displacement sensors have an advantage in repeatability, measurement errors can occur if the sensor itself moves out of place. The sensor must be firmly secured with a jig so that no change can occur to the angle and measuring distance during repeated measurements.
In the case of conventional sensors using the scale (pulse count) method, if the spindle moves abruptly due to vibration or other reasons, the response of the photoelectric sensor may be delayed, resulting in tracking errors. You will need to take measures against significant vibrations caused by any machines in the vicinity when installing these sensors.
Reflective laser displacement sensors
Reflective laser displacement sensors detect the position (distance) of targets at points. Therefore, single or multiple reflective laser displacement sensors can be used for a diverse range of applications. The type and number of sensor heads should be selected depending on the required detecting distance and accuracy, as well as installation location. The following section introduces typical applications and key points when considering the characteristics of their triangulation principle of detection.
During installation
In order to correctly receive the reflection of the emitted laser, the laser is emitted vertically from above the target. Depending on the sensor head selection and installation, the sensor may be installed at an angle. If necessary, consider the option of selecting a sensor head that can be installed at an angle.
Differences in target material and color
Significant differences in the material or color of the surface of targets can increase the rate of measurement errors. In general, measurement errors can be minimized by installing the sensor such that the line connecting the laser beam axis and the light-receiving axis of the light reflected from the target is parallel to the target’s borderline.
KEYENCE’s IL Series reflective laser displacement sensors can provide stable detection without tuning thanks to automatic adjustment of laser power, shutter time, and reception gain (amplification factor) in response to changes in target color and surface conditions.
Detection of concavities and narrow parts such as grooves in workpieces
If the part that you want to detect is surrounded by deep concavities or grooves, detection will not be possible if either the laser beam axis or the light receiving axis is blocked by an inner wall. When installing the sensor, you make sure that the light paths are not blocked, taking measures such as reviewing the detection points, installing a sensor head with a long detecting distance, or making the angle between the laser beam axis and light receiving axis smaller.
KEYENCE offers a sensor lineup that includes an ultra-long range sensor head that has a detecting distance of up to 3500 mm (137.80").
Thrubeam laser displacement sensors
Thrubeam laser displacement sensors produce a band of laser light on the light emission and receiving sides, and detect targets passing through based on how much light the target transmits. The width of the laser light of a thrubeam laser displacement sensor is determined based on detection requirements and the shape and size of the workpieces. The key points for installation and use are described below.
During installation
Correct alignment of light emission and receiving axes is critical for detecting targets. When installing the sensor, make sure the axes do not move even in the presence of any vibrations caused by nearby equipment. The axes should also be periodically checked to prevent errors.
Considering the ease of installation and use, it is important to select a laser displacement sensor that allows for easy inspection of the beam axis. KEYENCE’s thrubeam laser displacement sensors allow you to easily visualize the optical axis with an LED provided in the main unit. This facilitates optical-axis alignment during installation and changeovers.
Positional relationship with the target
When detecting the outer diameter of a bar-like or cylindrical workpiece, set up the sensor so that the band of laser light is vertically perpendicular to the longitudinal side of the workpiece. If the angle of the laser band is incorrect, an error will occur in the detection of outer diameter.
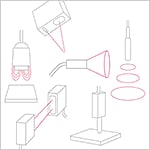
The Sensor Basics website introduces the working principles of nine different sensor types, their characteristics, and application examples, covering fiberoptic sensors, photoelectric sensors, vision sensors, and other essential sensors for modern factory automation, which includes, of course, laser displacement sensors and other laser sensors.
Frequently Asked Questions About Positioning Sensors
In most cases, optical-axis alignment is more difficult as the distance increases. Additionally, the optical axis can shift when the sensor is installed and used in a location where there is significant vibration. Alignment problems may occur, so periodic inspections are necessary. In consideration of this issue, KEYENCE’s thrubeam laser displacement sensors allow you to visualize the optical axis with an LED on the sensor. IG Series multi-purpose CCD laser micrometers have a position monitor in the main unit, and IB Series thrubeam type laser detection sensors have an alignment LED in the main unit, both of which indicate the position of the laser beam axis in a visible manner. You can directly see the state of the beam axis, which facilitates smooth setup and adjustment.
No. The IX Series image-based laser sensors uses a mechanism that is different from multiple sensor heads simultaneously emitting laser light. One IX Series sensor head installed over the workpiece, with multiple points specified within the field of view of the built-in camera, can complete laser emission and receipt for the heights at all specified points. This is possible because of the newly developed drive scan system, which detects heights at different locations using the following process:
1. The camera detects the position based on the target’s features and the system corrects the laser emission position.
2. The sensor head emits laser to the specified point using the high-accuracy MEMS mirror.
3. The reflected light is focused on the CMOS to calculate the distance.
A single sensor head performing the above process and control at high speed can stably and accurately detect heights at multiple points. Because the height of the reference plane is detected at the same time, the accuracy of the target’s detected height is not compromised by any tilt or misalignment of the target.
The IL Series sensor lineup includes an ultra-long range model, which can be installed up to 3500 mm (137.80") away from the surface of the target. For example, this laser sensor can detect sheet height in the clearance of a rolling machine without interfering with the machine. Hoop control during transfer of sheets or other workpieces is possible by providing the detected data as feedback to the machine. This model also supports applications in hot temperature environments, such as steel plate thickness measurement in high-temperature conditions, dimensional measurement of hot forgings, and positioning of robots that handle hot products.
![Error-free Displacement Measurement: Reflective Laser Displacement Sensors [Installation Guidelines]](/img/asset/AS_102775_L.jpg)
Error-free Displacement Measurement: Reflective Laser Displacement Sensors [Installation Guidelines]
This guide explains the triangulation principle of reflective laser displacement sensors and precautions for installation. It provides helpful information for appropriate introduction, installation, and use of these sensors, including the concept of reference points, errors deriving from installation and how to calculate such errors, and the flexibility and cost of installation, which is particularly important when considering introducing them.
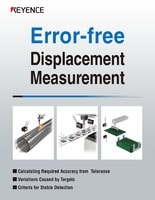
As a sequel to our well-received guide Error-free Displacement Measurement, this guide explains how to calculate required accuracy from tolerances, how to interpret the specifications listed in catalogs, how to work around errors deriving from different reflectance between workpieces, and sensor accuracy that conforms to the required tolerance, which is an indicator of stable detection.