Safety Laser Scanners
Safety laser scanners that meet the highest safety standards of Type3, SIL2, Category3, and PLd. Even though these are compact, they feature a wide detection range and are equipped with functions such as muting and bank settings. These devices are optimal for safeguarding machines such as automated guided vehicles (AGV) and robotic cells as well as a preferred alternative to hard guarding and safety mats.
Product Lineup
This series has impressive range (27.5′), is easy to integrate, and has multiple innovative features. It is the world’s first safety scanner with integrated cameras and detachable display for remote access. Other advancements include improved environmental resistance, network capability (CIP Safety, Profisafe, etc.) and quickly customized zones.
Features
Unmatched Detection
This safety scanner offers a large and flexible detection range (8.4 m 27.56' protection zone and 26 m 85.30' warning zone) to meet the needs of any safety guarding application. The SZ-V Series also features significant environmental resistance that provides stable detection and minimizes false trips caused by environmental factors.
Advanced Functionality
The SZ-V Series offers a variety of advanced features, including a separate display, multi-zone monitoring capabilities, cascading ability. etc. Plus, with an option for the World's First built-in camera, this safety scanner provides real-time visual feedback and compiles historical images/videos of scanner trips.
Ease-of-Use
The SZ-V Series features a free, dedicated software that allows for customizable zone creation and scanner setup in minutes with a simple 5-step process. Plus, the SZ-V Series offers safety networking capabilities, allowing for remote monitoring from anywhere.
A safety laser scanner is a sensing device designed to protect personnel from injury. These devices are most commonly used in factory automation for machine safeguarding. This device scans an area and if a person or object is detected, a signal is sent to stop the nearby machine or hazard to prevent injury. Unlike typical laser sensors, safety laser scanners monitor themselves through redundant signals and will stop the hazard (ex. machine) if an internal fault is detected. These devices are now commonly used to replace pressure sensitive safety mats, hard guarding, and light curtains.
How do Safety Laser Scanners work?
A safety laser scanner uses a laser that "scans" an area and when a person or object is detected, a signal is sent to stop the nearby machine or hazard. Unlike typical laser sensors, safety laser scanners monitor themselves through redundant signals and will stop the hazard (ex. machine) if an internal fault is detected.
What are Safety Laser Scanners used for?
Safety laser scanners are most commonly used in manufacturing for machine guarding to protect personnel from injury. Safety laser scanners offer non-contact protection while scanning a large area. The protection (safety) zone is also 100% customizable. This technology often has clear advantages over hard guarding, fencing, or pressure sensitive safety mats.
Benefits of Safety Laser Scanners
Safety laser scanners allow for a 100% customizable protection zone, even in complex areas. Lack of customization is a common issue with safety mats. The non-contact detection of a safety laser scanner also minimizes the risk of breakage from falling objects and impact, another common problem with safety mats.
With a safety laser scanner, there is no limitation to the shape of the protection zone so long as the shape does not exceed the detection range. The protection zone can also be changed according to the layout of the machinery. Safety laser scanners are also compact, making them a viable alternative in places where safety light curtains cannot be used. Using multiple safety laser scanners is possible to eliminate any blind spots, ensuring complete detection in any area of any size.
As it relates to longevity and failure, the very nature of safety mats makes them prone to internal wire breakage caused by items being dropped on them and people stepping on them. The protection range is also limited to the shape of the safety mat, leaving some areas undetected. On the other hand, safety laser scanners detect any operators in the protection zone without contact, making them immune to damage from falling objects and people stepping on top.
Safety laser scanners can be installed in facilities where light curtains are not suitable, and the muting function makes it possible to minimize undetectable areas.
For example, when detecting access into a large entry point of a production line, using the light curtain’s muting function may prevent detection of entry as products are passing through.
Safety laser scanners, however, enable flexible and customized configuration of the muted area. With only the exact shape of the item being muted, other open areas that could pose a danger are eliminated.
Safety laser scanners are not restricted by where they can be installed or what areas they can cover. This means safety laser scanners can be used wherever they offer the best protection inside the factory.
Multiple protection and warning zones can be set up for each bank. With a maximum of 32 configurable banks, users can select the most appropriate zone by using external signals. Three levels of control can be set up through selective use of protection zones and warning zones.
“Bank” refers to the combination of a protection zone and a warning zone. Safety laser scanners are capable of handling multiple banks, and users can switch between these banks using external signals to select the most suitable protection zone at that particular time. This is called the bank switching function. Models that can be used to register up to 32 banks allow configuration of one protection zone and two warning zones for each bank.
KEYENCE’s safety laser scanners are equipped with a function that monitors the bank switching order and triggers an error when a bank switching command is issued out of order. This prevents machine operation with an unintended protection zone selected. These functions are useful safeguards for automated guided vehicles (AGV) and collaborative robots (cobots).
Safety Laser Scanner Case Studies
AGV safeguards
Automated guided vehicles (AGV) require a safety device that can switch the protection zone according to the surrounding situation.
The SZ-V Series and the SZ Series both include the bank switching function for constantly detecting the travel direction of the scanner. The bank switching function is used to specify the protection zones and warning zones configured as banks. By switching banks according to the direction of travel, the safety laser scanner can continuously monitor its surroundings.
This ensures the AGV stops when the safety laser scanner detects a person or object on the course ahead. It also disables AGV startup when near a person or object. Selective use of protection zones and warning zones make it possible to issue an alarm warning whenever a person or object enters a warning zone, and stop the AGV if a person or object enters a protection zone.
Safeguards for six-axis robots without safety fences
Entering the movable range of an operating robot with no safety fence is extremely dangerous for operators, so strict safeguards must be put in place. It is possible to control the system so that the robot does not start up until all operators are outside of the protection zone. For example, a robot can be slowed down when an operator comes near the robot and stopped when the operator enters the robot’s movable range. Startup can also be prohibited while an operator is working in the movable range. In situations where robot operation is necessary even while an operator is in the protection zone, such as for maintenance, the safety function can be temporarily disabled.
Such a control system can be created using a communication-capable scanner.
Safeguards for rolling machines: Unwinding devices
With most rolling machines, operators manually feed the materials, set up the rolls, and clean the machine. For this reason, reliable safety measures are necessary to ensure that the roller is completely and unmistakably stopped while operators perform work.
The SZ-V Series and the SZ Series reliably ensure the safety of operators working inside the safety perimeter. When the rolling machine is stopped and an operator enters the safety fence, the safety laser scanner detects the operator’s presence. Rolling machine startup is disabled while the operator is inside the safety perimeter.
Combine this with a safety interlock switch (GS-50 Series), this creates a safety system that prevents rolling machine startup until the operator finishes working inside the safety perimeter, leaves the space, and closes and locks the door again.
Sensors designed to meet ISO, IEC, and other international standard requirements are called safety sensors. Certified safety sensors that use laser scanners are called safety laser scanners.
To become a certified safety laser scanner, devices must meet the following international standard requirements.
IEC 61496: Type 3
IEC 61508: SIL 2
ISO 13849: PLd, Category 3
Both the SZ-V Series and the SZ Series of safety sensors are certified as having met these high safety standards. This section offers a closer look at the certified standards of these two sensor series.
What is the IEC 61496: Type 3 standard?
This product safety standard focuses on electro-sensitive protection equipment (ESPE), including safety sensors such as safety laser scanners, that electrically detects human bodies and outputs control signals for protecting workers while a machine is in operation.
Safety sensors are classified by safety level, and each type must incorporate a design and structure that prevents hazardous situations in the event of a component failure. Type 4 devices offer the highest level of safety. Each type also has separate environmental requirements such as noise resistance (EMC), temperature and humidity resistance, mechanical durability (against vibrations, shocks, etc.), water resistance, and power voltage resistance characteristics.
The requirements for each type are outlined below.
IEC 61496-2 (Type 2, 4): Detection of human bodies based on the interruption of a laser beam between a transmitter and receiver.
IEC 61496-3 (Type 3): Detection based on the reflection of laser light.
IEC 61496-4 (Type 4): Detection based on image sensing technology.
Safety laser scanners are categorized as Type 3 devices. Type 3 devices are also required to meet requirements for minimum detectable target reflectance (1.8%), ambient light resistance (resistance to various types of ambient light), and resistance to the effects of dirt, backgrounds, and obstructions. SZ-V Series and SZ Series devices meet all Type 3 requirements.
What is the IEC 61508: SIL 2 standard?
The IEC 61508 international standard sets forth the requirements for the functional safety of electrical, electronic, and programmable electronic safety-related systems. SIL is an abbreviation for Safety Integrity Level, which is the specified safety level for safety functions. As the measure of the safety performance of a system, the SIL indicates the probability of the system failing to operate in response to an operation request (dangerous failure rate per unit of time). There are four specified SIL, SIL 1 to SIL 4. Safety laser scanners are required to meet SIL 2 requirements. For SIL 2, the dangerous failure rate per unit of time must be 10⁻⁷ or more but less than 10⁻⁶, and both SZ-V Series and SZ Series devices meet this strict requirement.
What is the ISO 13849: PLd, Category 3 standard?
This section introduces PLd and Category 3, the two ISO 13849 requirements that the SZ-V Series and SZ Series have met.
What is PLd?
The “PL” in PLd stands for Performance Level, which specifies the ability of a control system to perform safety functions under foreseeable conditions. The parts that execute the safety function of a machine are called the safety-related parts of the control system, and the classification level used to regulate the performance of these safety-related parts is called the performance level (PL). A system’s PL must always be equal to or higher than the system’s required performance level (PLr). Safety laser scanners with a performance level of “d” (PLd) are rated as having a dangerous failure rate per unit of time of 10⁻⁷ or more but less than 10⁻⁶ (0.00001% to 0.0001%).
What is Category 3?
For safety-related parts, the safety category refers to the structure (architecture) of the part. Category 3 is one of those safety categories. Safety-related parts ensure the safety of a machine, but the appropriate structure varies depending on the purpose of the machine, the level of danger, the size of the machine, and the frequency of use. There are four different safety categories (1 to 4), and safety laser scanners must meet Category 3 requirements. Category 3 requires that the overall safety functionality of a device is not impaired even if a failure occurs in any part of the safety function.
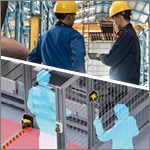
This site includes information on machine safety standards and managing risk. Learn about ISO international standards, risk assessment, and other important safety topics.
Frequently Asked Questions About Safety Laser Scanners
A safety laser scanner serves three major purposes: area protection, access protection, and collision prevention.
For area protection, the safety laser scanner is installed horizontally to monitor a hazardous zone. For example, area protection may involve checking for any remaining operators and preventing the machine from being restarted if detected.
For access protection, safety laser scanners are commonly installed vertically to detect access into a hazardous zone and stops machine operation if entry is detected. Safety laser scanners can be used in place of light curtains, which need pillars on both sides of the entry point, to detect access.
Collision prevention is a function used when the safety laser scanner is installed on an automated guided vehicle (AGV). The scanner detects nearby workers to prevent collisions. Safety laser scanners can also be used for collision prevention with rail-guided vehicles (RGV) and forklifts.
Safety laser scanners are reflective sensors that use laser light. They can be installed anywhere and for any protection zone.
This gives them an advantage over light curtains in terms of available installation locations. Aligning the optical axis during installation is also incredibly easy. Even complex-shaped protection zones can be easily set up using the intuitive software.
Additionally, compared with safety mats, safety laser scanners are not at risk of being damaged from falling workpieces. Safety laser scanner protection zones can be set freely, so layout changes can be implemented with ease. When changing the layout, there is no need to have a stock of safety mats of different sizes and shapes for creating different protection zone shapes.
Compared with other safety devices, safety laser scanners are less restricted in terms of installation location and protection zones. Installation is easy and the risk of failure is minimal, making them safety devices that offer efficient safeguards.
One of the most common causes of accidents near robots is activation (reactivation) of the machine while someone is still inside the safety fence. Blind spots tend to increase near larger robots, and the need for measures to secure such blind spots is clearly defined in various standards (including ISO 10218-2).
Using a safety laser scanner makes drawing up a protection zone simple. The functions for easily drawing zones according to a current layout and for drawing zones customized to a specific location both allow for simple protection zone setup. The maximum protection zone is also large. Using multiple safety laser scanners can completely eliminate blind spots.
With the help of such functions, safety laser scanners can easily detect workers without having to change the layout around the robot.
Some safety scanners offer safety networking capabilities. Common communication protocols used by safety scanners include CIP Safety, PROFIsafe, etc. Safety networking allows for the scanner to communicate directly with a safety PLC, enabling remote monitoring and data retrieval. Additionally, networking with a safety scanner offers a wide variety of beneficial features, including dual zone control, simplified wiring, and an overall reduction in cost relative to other machine guarding methods.

This guidebook introduces a wide range of safety information, including machine safety standards (for manufacturing equipment and other machines), the Performance Level (PL) classification used for defining risk assessment and safety factors, and specific safety devices.
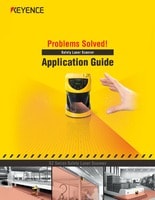
Browse a collection of actual SZ Series application examples with a focus on six different types of problems regarding safety measures. This guide is a must-read for anyone experiencing problems with safety mats or light curtains, or having problems selecting or installing safety devices.