Flow Sensors / Flow Meters
A flow sensor/meter for liquid and gas. KEYENCE has developed various clamp-on types to enable stable flow rate measurement with no pipe modification. These devices can be used on small tubes to large pipes. The lineup also includes electromagnetic and Coriolis flow sensors as well as environmental resistant and sanitary types.
Product Lineup : Liquid Flow Rate
The FD-H Series clamp-on flow sensor is easily installed, without any pipe modification, by simply clamping to the outside of a pipe, tube or hose. This series provides stable flow rate measurement regardless of the pipe or liquid. In addition to metal and hard plastic piping, hoses (including high-pressure hoses) can also be supported. This product can not only measure the flow rates of various liquids such as water, DI water, oil, chemicals, and coolants but can also tolerate bubbles, high temperatures, and highly viscous liquids. Connecting a concentration sensor and temperature sensor allows for the centralized management of multiple parameters, helping improve product quality, and decrease costs.
Features
Countless Opportunities for Process/Machine Improvement
Supports Any Pipe, Type of Liquid, and Liquid Condition
KEYENCE clamp-on flow sensors perform detection from outside the pipe for a wide variety of applications. Now it is possible to monitor liquids with bubbles, high temperatures, and high viscosities.
Unmatched Features
A detachable display allows for remote monitoring while also clearly displaying current values, real-time graphs, historical data and more. Universal connectivity is achieved with a choice of control outputs, analog outputs, and IO-Link. Additional features include high environmental ratings (IP65 & IP67), a built-in diagnostic function, and accuracy of 3% of R.D.
Extend Beyond Flow Sensing to Understand the Full System
Connecting other sensors to the FD-H Series allows for the continual recording and management of multiple parameters including liquid flow rate, concentration and temperature.
Compatible with a variety of pipe materials and liquids, the FD-Q Series Clamp-on Flow Sensor can detect the flow rate of a liquid without the need for any pipe modification. This device enables the detection of a wide variety of liquids, including water (and pure water), oil, and chemicals. Detection is possible on both metal and resin pipes up to 2" in diameter. Unlike conventional sensors, installation and operation are also easy on high-pressure pipes. Costs are significantly reduced with the minimal installation required and the completely non-wetted design eliminates the risk of pressure loss or increased maintenance. Additionally, the large indicator provides real-time status information.
Features
Easy to Install for Any User
FD-Q can be mounted quickly and easily with only a screw driver, no pipe modifications necessary.
- Mount in 60 seconds without any pipe modification
- Clamps on to the outside of a pipe with 6 standard screws
- Install flow sensor without shutting the machine down
Installing a Conventional Flow Sensor
Extremely difficult, requiring special knowledge, tools, and machine downtime.
Installing FD-Q Series
Anyone can easily mount with just a screwdriver.
Compatible With Countless Flow Setups
FD-Q can detect and handle all sorts of fluids, pipe materials, and pipe sizes.
Detectable fluids
- Detect virtually any type of liquid including: Water, oils, chemicals, consumer products, etc.
Compatible pipe materials
- Detection is possible through both metal and resin pipes
- Compatible pipe sizes include 1/4"-2"
The FD-X Series Clamp-on Micro Flow Sensor has a flow rate resolution of 0.1 mL/min (and a shot amount resolution of 0.001 mL). The device does not come into contact with the liquid, preventing problems such as pressure loss and clogging. The non-contact design also means the device is not affected by the properties of the liquid (ex. viscosity). Even coating/filling applications of grease, adhesives, flux, sealants, chemicals, and other liquids are possible with the FD-X series. The design also prevents pressure drops, enabling flow rate measurement with no adverse effects on equipment conditions, such as jetting and spraying functions. Also, this clamp-on technology means there is no pipe cutting or modification required.
Features
Utilize Everywhere
- Detect flow rates as low as 0.1 mL/min or shot amounts as low as 0.001mL
- Any liquid flow rate can be monitored including:
Viscous greases, chemicals, and sanitary liquids - Compatible with metal pipes and resin tubes from 0.12" - 0.5"
Zero Impact on Process
- Simply clamp the flow sensor to any pipe or tube
- Completely non-invasive
- No machine downtime or risk of clogging, pressure loss, or contamination
KEYENCE's FD-R Series Clamp-on Flow Meter is designed for pipes as large as 8". Installation is easy and requires only a screwdriver. The device can be mounted to a variety of materials including stainless steel, iron, copper, PVC, and resin. Both flow and temperature monitoring is possible for a wide variety of liquids—from water (including pure water) to oil, chemicals, and high-pressure liquids—at temperatures between -4°F and +248°F. The device does not come into contact with the liquid, so there is no risk of liquid-based corrosion or degradation, reducing maintenance time and costs. The rugged metal construction includes an easy-to-read indicator light, and data can be recorded directly on the device. The IP69K enclosure rating and NEMA4X compliance make this sensor both highly reliable and convenient for indoor and outdoor use.
Features
Mounting and Integration
- Clamp-On the Outside of a Pipe
- No Pipe Modification
- No Downtime
- Easily Secure with 4 or 6 Screws
- Bracket Ensures Correct Mounting by Anyone
Versatility for Any Situation
- Monitor Water, DI Water, Oils, Chemicals, Product, etc.
- Mount to Stainless, Iron, Copper, PVC, Resin, etc.
- Precise Monitoring with Accuracy of ±2.0% of RD
- Integrated Temperature Monitoring
- AC/DC Compatibility
The FD-M Series Non-Wetted Electrode Electromagnetic Flow Sensor is the first factory automation flow sensor to adopt a free-flowing structure. Unlike floating-element and paddlewheel devices, the free-flowing structure of the FD-M Series has no moving parts or obstructions in the flow pipe, greatly reducing the risk of clogging. With no moving parts, the sensor is not subject to mechanical wear, which ensures a long service life. There is also virtually no pressure loss in the pipe, so the pump uses even less energy. Unlike conventional electromagnetic systems, this device detects liquid from outside the pipe, making it highly resistant to insulating deposits inside the pipe while minimizing maintenance. Two sensor types are available: one with a separate amplifier that allows flow rate monitoring using the LEDs on the sensor head and one with an integrated amplifier and a dual-row digital display for easy setup.
Features
No Obstructions
The FD-M Series leaves behind conventional flow sensing technology where paddle wheels or other obstructions can cause clogging or incorrect monitoring. The FD-M has no moving parts allowing liquid to flow freely while monitoring.
Versatility
The FD-M is commonly used in a wide array of industries such as grinding, injecting molding, and welding. It is more tolerant than conventional sensors to variations in temperature and fluid type. Additionally, the FD-M's analog capability broadens the scope of possible applications.
Product Lineup : Gas Flow Rate
The FD-EP Series simultaneously monitors air flow and pressure to provide a full breakdown of pneumatic machine performance. The FD-EP Series also features built-in predictive maintenance modes specific to a variety of machines and applications (cylinders, seating confirmation, air blow, etc.) to identify common pneumatic equipment issues. Additionally, with its free flowing internal structure, the risk of clogging and pressure loss is eliminated.
Features
Dual Sensing of Flow and Pressure
Air pressure and air flow in a single unit opens up full understanding of pneumatic equipment on the machine. Knowing pressure and air flow at the same time allows us to predict component failures before unexpected downtime occurs. With 4 built-in application modes programmed into the sensor, increased machine uptime will be more achievable.
Pressure × Flow
Built-In Predictive Maintenance Modes
The FD-EP Series features four built-in predictive maintenance modes to manage pneumatic equipment and diagnose potential component issues. These predictive maintenance modes include cylinder status monitoring, suction conveyance, seating, and air blow. The FD-EP monitors the condition of these processes in order to improve pneumatic equipment productivity and identify potential abnormalities.
Cylinder Status Monitoring
Suction Conveyance
Seating
The FD-EC Series Clamp-On Air Flow Sensor easily mounts to the outside of any tube, eliminating the risks & headaches found with conventional in-line flow sensors. With its ability to monitor a wide range of flow rates and clamp on to any tube, the FD-EC Series provides significant versatility. This series also features a high-precision display that clearly conveys the status of the flow meter, allowing for straightforward operation.
Features
Risk-Free Installation
With its ability to clamp-on to the outside of any tube, the FD-EC Series Air Flow Sensor eliminates the risk of pressure loss, clogging, air leakage, and contamination commonly caused by convention in-line air flow sensors. Because no tube modifications are necessary for installation, the FD-EC Series eliminates downtime and the need to shut off the air supply.
Conventional Unit
- Clogs due to multi-layer mesh structure
- Leaks from coupling
FD-EC Series
- Zero risk of pressure loss, clogging or contamination
- Zero air leakage
Ultra-Compact and Lightweight
With its ultra-compact style body, the FD-EC Series can be mounted anywhere, even in areas with limited space between air tubes. This series is also incredibly lightweight, eliminating the need for additional mounting brackets.
The FD-G Series Clamp-on Gas Flow Meter can be easily installed from outside the pipe with only a screwdriver. The clamp-on design greatly reduces installation costs by eliminating the need for pipe modification. Detecting flow from outside the pipe eliminates the risk of restricting or blocking the flow of gas. It also eliminates the risk of leakage from new fittings. The device is compatible with stainless steel and iron pipes from—3/4" to 8"—and can measure compressed air, nitrogen, and other gases. The high-accuracy measurement, paired with a minimum sensitivity of 0.018 CFM, can be utilized for both large flows and incredibly small leaks. The high-definition display can also show both the total flow rate and the current flow rate for a set period, at the same time. Necessary functions for air management are also included, such as automatic leak volume measurement and monetary conversion.
Features
Optimize Compressed Air Usage
- Determine a baseline for air usage at your facility
- Monitor specific machine drop points or branch pipes
- Identify cost-saving actions such as replacing valves, optimizing your compressor's loading period, or patching leaks
Simple Clamp-On Installation
- Mount in minutes with no special tools or knowledge
- Completely non-invasive flow meter design means no added leakage points
- Compatible pipe sizes include 0.75"-8"
Product Lineup : Air Quality Multi-Sensor
The MP-F Series Air Quality Multi-Sensor simultaneously monitors air flow, pressure, temperature, and humidity, for a complete breakdown of pneumatic machine air quality and consumption. Having an increased understanding of machine air usage allows for more stable machine operation, improved product quality, and ultimately cost savings.The MP-F Series also offers multiple options for data gathering (including the built-in display and dedicated software). Additionally, the unit provides clear visualization of air and electricity consumption. The MP-F Series also includes a built-in shut off valve, which allows users to control their air supply needs when machines are not in use.
Features
All-In-One Monitoring
The small body of the MP-F Series contains multiple sensors, allowing for full comprehension of machine air quality and consumption. Better understanding the condition of machine air quality helps ensure the stability of pneumatic equipment, identify abnormalities, and increase lifespan of critical components.
-
1Humidity sensor
-
2Flow/Temperature sensor
-
3Pressure sensor
Easily Visualize Consumption
The MP-F Series offers multiple options to gather data needed to reduce costs and make informed decisions. The easy-to-navigate display offers a clear and complete understanding of all air-related variables, allowing for straightforward air quality and consumption analysis. Long-term data can also be downloaded through the dedicated software with a standard USB cable and laptop.
Flow meters, also known as flow sensors, are used to measure the flow rate of a liquid or gas. There are a variety of different types of flow meters, including ultrasonic, electromagnetic, Karman vortex, paddlewheel, floating element, thermal, and differential pressure types. Flow meters that require no moving parts in contact with the target liquid are particularly effective in avoiding potential problems. For example, ultrasonic meters—also known as clamp-on systems—can be installed from outside the pipe for completely non-wetted measurement, preventing any risk of adverse effects on the liquid and eliminating the need for piping work. Electromagnetic meters detect flow via electromotive force created through electromagnetic induction. Models that use an electrode outside the water outlet are most effective. Meters that use the Coriolis method measure the backward force created by the flow of liquid through an oscillating U-shaped pipe. Alternatively, thermal meters measure the flow rate by looking at the amount of heat the liquid removes from a heating element.
Benefits of Flow Sensors / Flow Meters
The manufacturing of products can involve a wide variety of liquids. To ensure quality control, the liquid is monitored using a flow meter and then managed/analyzed accordingly to improve or stabilize product quality. Understanding the different types of flow meters plays an important role in performing sufficient fluid management and analysis.
Using a flow meter for managing liquid flow enables data acquisition for alarms, diagnosis, and analysis. It also allows for management of minute flow rates such as equipment discharge and spray volumes, and management of air, nitrogen, or argon gas supplies based on instantaneous and total flow rates. Flow meters equipped with an analog output can respond flexibly to control and manage needs by transmitting alarm output and diagnostic/analysis data to a PLC or PC. Clamp-on flow meters, which use non-wetted methods that do not adversely affect the liquid, are also capable of measuring very low flow rates at high speeds. This is often necessary for controlling release agent, disinfectant alcohol, and flux application amounts. Mass flow sensors are not easily affected by temperature or pressure, making them suitable for the management of gases.
Flow control using a flow meter enables both predictive maintenance and superior device protection, such as when an optimum temperature range is specified or a correct amount must be used for cooling water circulation. Flow control makes it possible to prevent any deterioration in quality or malfunctions with equipment due to improper cooling.
Quick detection of a decrease in flow rate makes it possible to immediately perform predictive maintenance to avoid adverse effects on production or equipment. This means flow control using a flow meter is essential. A flow meter with two outputs enables the output of both a predictive alarm and the main alarm for proper maintenance before jigs or equipment becomes damaged. Monitoring the conditions of filters and strainers is also important for detecting clogs that may reduce flow. In other cases, bent or clogged pipes may not show a change in pressure, only a decrease in the flow rate. Using a flow meter in addition to a pressure sensor makes it possible to detect problems in the piping quickly for immediate response.
Manufacturing sites often use argon gas for welding, nitrogen gas for oxidation-prevention and heat treatment, and various other resources such as hydraulic oil and coolant. Using a flow meter for flow control makes it possible to visualize the amounts of resources used and to conserve energy (which reduces costs).
Flow meters capable of managing instantaneous and total flow rates simultaneously can detect abnormal flows. These devices can also gather data to determine possible reductions in the consumption amounts based on per-hour usage. Also, if the flow meter has no moving internal components, reductions in pressure due to clogging or other problems can be eliminated, contributing to greater energy conservation with no unnecessary load on pumps. Clamp-on flow meters can also be installed without having to cut piping, eliminating the risk of liquid and air leakages due to added pipe seams.
Flow Sensor / Flow Meter Case Studies
Equipment requiring liquid management (coolant, cleaning fluid)
Equipment requiring liquid management and flow monitoring include injection molding machines (mold coolant flow control), die-casting machines (coolant and mold release agent flow control), grinding machines and cutting machines (coolant flow control), sputtering systems (coolant flow control), and spot welding machines (coolant flow control). Using an applicable flow meter or flow sensor for flow management stabilizes product quality and prevents potential problems with equipment.
Equipment requiring liquid management (oil, coating solutions, chemical solutions, etc.)
Because liquid flow rates and process management are closely intertwined, flow meters and flow sensors are also useful in controlling the flow of liquids other than coolant and cleaning fluid. For example, flow control is also necessary with high-frequency quenching equipment (quenching fluid flow control), lapping/polishing/CMP equipment (slurry), dispensing equipment (flux, hot-melt, ink, grease, adhesives, painting solutions, coating agents, resist solutions, mold release agents, etc.), precision presses (lubricant, etc.), two-component mixers (pre- and post-curing agent liquids, water, printing paint, chemicals, emulsions, adhesives, etc.), cutting machines (for checking cutting oil amounts, etc.), concrete mixers and manufacturing equipment (water volume being mixed with materials), and flue gas neutralization equipment (water and chemical solutions used during smoke evacuation).
Equipment requiring gas flow control (nitrogen, oxygen, air, etc.)
Flow meters and flow sensors are used in processes and machines requiring the flow control of gases such as nitrogen, oxygen, and air. This includes reflow furnaces (nitrogen (N2) flow control to prevent oxidation), quenching furnaces (nitrogen (N2) supply control to prevent oxidation), chip component conveyors (for checking airflow during chip component absorption), electronic component packages (management of enclosed gas (nitrogen) to prevent oxidation), ionizers (air purge flow control), and painting robots (paint (liquid) and air (gas) management).
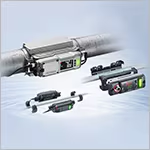
Learn basic information such as the principles adopted in various types of flow meters—including electromagnetic, Coriolis method, and ultrasonic devices—along with measures to prevent problems with piping and measurement. This site provides a wide variety of tips for ensuring smart flow management.
Frequently Asked Questions About Flow Sensors / Flow Meters
Air bubbles can enter the pipe with the liquid or be formed in the pipe due to impurities or other factors. Bubbles can cause Karman vortices to occur in vortex flow meters, and ultrasonic wave propagation can be obstructed in conventional ultrasonic flow meters, causing the flow meter to malfunction. Generally speaking, flow rates can be measured with no effects from air bubbles when using a meter that measures using the Coriolis method. In recent years, ultrasonic wave flow meters have also begun using stronger ultrasonic signals to ensure adequate signal propagation, even if bubbles are generated. Some ultrasonic flow meters are also able to cancel out the effects of air bubbles or to generate an alarm if air bubbles are detected.
For flow meters that use a standard wetted electrode, insulating deposits inside the pipe can make measurement impossible. Conventional electromagnetic flow meters are also prone to such problems. Flow meters that use capacitive detection with electrodes on the outside of the pipe are effective at preventing these kinds of adverse effects. Fully penetrating electromagnetic flow meters detect liquid from outside the pipe, allowing for stable detection even if the pipe is covered with insulating deposits. Naturally, badly contaminated pipes will require cleaning or other maintenance because of the potential adverse effects on the equipment.
The effects of frequent bending, branching, or diameter variations can result in an uneven velocity of flow in the liquid. This may result in significant measurement errors. To ensure a uniform velocity distribution, a straight section of a sufficient length must be provided on the upstream side of the flow meter or flow sensor. This straight section should be at least 5 times longer than the diameter of the flow path, or 20 times longer if severe deflections or swirling currents exist. If significant measurement errors still exist, consider installing a valve or aperture.
As liquid flows through piping, valves are opened/closed and as connected pumps and other equipment operate, vibrations can be generated. Such vibrations and other noise can result in measurement errors. Karman vortex-type and Coriolis-method devices are often affected by vibrations and are likely to suffer from incorrect measurements. Electromagnetic and ultrasonic devices, however, are virtually unaffected by vibrations. In particular, ultrasonic flow meters that are capable of transmitting and receiving ultrasonic waves at high frequencies are less susceptible to vibrations and noise to ensure stable flow measurement.
Click here to enter the Flow Meter Selection Site. Enter your information and a product expert will send you a recommended parts list.
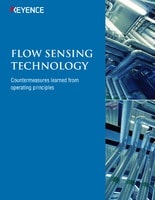
Get help handling flow management problems by learning about the various types of flow meters and the principles they adopt. This document includes essential information such as countermeasures for problems related to scale, rust, sludge, and other factors, and how to select the best flow meter for specific piping and liquids to avoid potential problems.
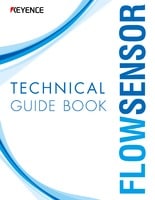
Learn the basics of using flow meters in factories, the factors that can lead to problems, and essential techniques for ensuring stable flow management.
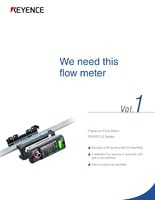
Read all about clamp-on ultrasonic flow meters that can be installed with no equipment downtime or piping work needed. Discover solutions to various conventional problems and get detailed, easy-to-understand information on the advantages of clamp-on devices.