Digital Microscopes
Anodized Aluminum Processing Observation and Measurement Using Digital Microscopes
This section provides an overview of anodized aluminum processing and introduces observation and measurement examples using a digital microscope.
A thin oxide film (approximately 2 nm) naturally forms on aluminum when it comes into contact with air. Therefore, it is commonly believed that aluminum does not rust easily.
However, this film is extremely thin, so chemical reactions may cause aluminum to corrode depending on the environment. Anodized aluminum processing is a type of surface processing in which this oxide film is artificially formed on aluminum.
What Is Anodized Aluminum Processing?
A : Plating layer B : Growth film C : Penetrating film D : Aluminum material
Half the anodized aluminum film grows on top of the aluminum surface. The other half penetrates into the aluminum surface.
Anodized aluminum processing is a type of surface processing in which an anodic oxide film is formed on the surface of aluminum.
Plating is another type of surface processing, but whereas plating causes a film of another metal to form on the aluminum surface, anodized aluminum processing causes a growth film to form on top of and a penetrating film to form underneath the aluminum surface.
Get detailed information on our products by downloading our catalog.
View Catalog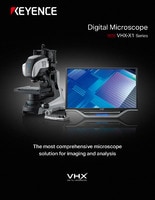
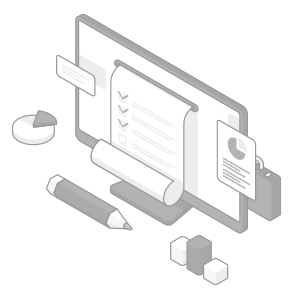
Anodized Aluminum Formation Process and Structure
A : In air B : In electrolytic solution
C : Original aluminum surface D : Barrier layer
Passing an electric current through aluminum causes the microscopic dents and protrusions on the surface to dissolve (penetrating into the surface) while at the same time causing an oxide film to form. As time passes, a 3D structure known as a cell forms.
-
1In air, an oxide film approximately 2 nm thick forms naturally.
-
2The barrier film grows.
-
3Holes 10 to 20 nm thick open up.
-
4Oxidation and the dissolution of the film proceed simultaneously, elongating the holes.
-
5The film grows proportionally to the time electrolysis is applied.
We’re here to provide you with more details.
Reach out today!
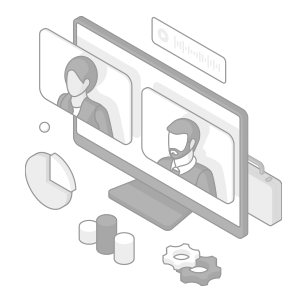
Colored Anodized Aluminum and Hard Anodized Aluminum
Normal anodized aluminum can be colored by sealing organic paint in the microscopic holes formed on its surface. Colored anodized aluminum is not commonly used in building materials because while it is resistant to easy removal of the coloring, it is vulnerable to ultraviolet rays and heat.
With a thick oxide film, hard anodized aluminum is harder than normal anodized aluminum. Hard anodized aluminum is used in sliding parts (shafts and rolls), automotive engine parts, aircraft parts, and similar applications. This is because it has excellent hardness, wear resistance, corrosion resistance, insulation properties, and heat resistance.
Comparison item | Normal anodized aluminum | Hard anodized aluminum |
---|---|---|
|
White or colored |
Gray (generally cannot be colored) |
|
Approximately 200HV |
400HV or more |
|
5 to 25 µm (0.000197″ to 0.000984″) |
20 to 70 µm (0.000787″ to 0.002756″) |
|
Building materials, household goods, decorations |
Sliding parts (shafts and rolls), automotive engine parts, aircraft parts |
We’re here to provide you with more details.
Reach out today!
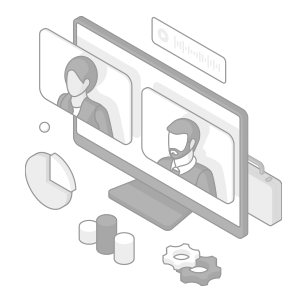
Advantages and Disadvantages of Anodized Aluminum Processing
This section explains the advantages and disadvantages of anodized aluminum processing.
Advantages
- Corrosion resistance : The corrosion resistance is improved.
- Insulation properties : The insulation properties are excellent because the oxide film does not conduct electricity.
- Thermal conductivity : The thermal conductivity is a third that of aluminum that has not undergone anodized aluminum processing.
- Hardness : Although normal aluminum has a hardness of 20HV to 150HV, aluminum that has undergone anodized aluminum processing obtains a hardness of 200HV or higher.
- Coloring : Various colors can be applied to the microscopic holes on the surface.
Disadvantages
- Heat resistance : The surface will crack or peel in environments whose temperature exceeds 100°C (212°F).
- Fragility : The surface is not flexible, so it will crack or peel if bent.
We’re here to provide you with more details.
Reach out today!
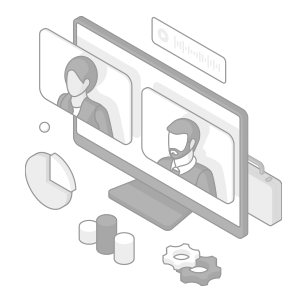
Anodized Aluminum Processing Observation and Measurement Examples Using a Digital Microscope
These are the latest examples of anodized aluminum processing observation and measurement using KEYENCE’s VHX Series 4K Digital Microscope.
Surface observation after anodized aluminum processing
Optical Shadow Effect Mode can be used to visualize surface scratches that are difficult to see with normal observation.
VHX-E500, 1000×, coaxial illumination, normal image
Optical Shadow Effect Mode image
Surface observation after black anodized aluminum processing
VHX-E100, 100×, ring illumination
left : Optical Shadow Effect Mode image, right : normal image
Optical Shadow Effect Mode provides a clear picture of the surface texture.
Measurement of the thickness of the anodized aluminum film
VH-Z500, 3000×, coaxial illumination
Conventional SEMs were utilized for this measurement; however, sample preparation required a significant amount of time.
Building material scratch observation after anodized aluminum processing
VH-Z20, 200×, ring illumination, normal image
VH-Z20, 200×, ring illumination, image after glare removal
The glare removal function allows for observation without glare.
VHX-E100, 100×, ring illumination, 3D image
The 3D function enables defect cause identification by showing how scratches are formed.
Get detailed information on our products by downloading our catalog.
View Catalog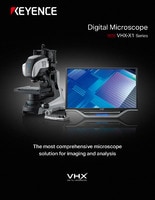
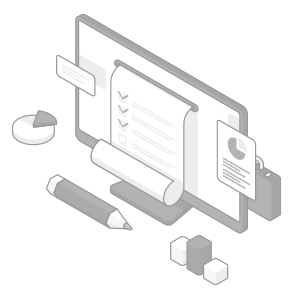