Multisensor Measurement System
Benefits of a Multisensor Measurement System
As manufactured parts become more complex with tighter precision requirements, multisensor measurement systems are essential for keeping pace. These systems perform 2D/3D and GD&T dimensional measurement using multiple different sensors, all in one go. Because of its flexibility, these systems enhance inspection efficiency, simplify measurement processes, and reduce the need for multiple systems.
Multisensor measurement systems are used across every industry for these reasons alongside their adaptability for measuring parts. In the following, we’ll explore the definition of a multisensor measurement system and its versatility across industries and applications.
What is a Multisensor Measurement System?
A multisensor measurement system is a tool that combines multiple types of sensors, –touch, vision, laser, etc.—into a single machine. In contrast, single-sensor machines are more limited and only rely on one type of sensor.
These systems can work to acquire precision dimensional measurement data, GD&T and CAD comparison used for multifaceted measurements like profiles with various heights and angles. Having multiple sensors means these tools offer versatility for all types of applications and adaptability for different types of measurements.
Using Multisensor Measurement Systems in Various Industries
A multisensor measurement system is convenient because of how many industries it can be used in, thanks to the fact these systems tackle parts with a wide range of shapes, sizes, and surfaces. Here are a few examples:
Medical Multisensor Metrology
In the medical device industry, a multisensor system is beneficial for inspecting complex shapes and sensitive devices efficiently. A multisensor measuring system uses a probe to trace curves and edges without adding excessive pressure, lasers for quick flatness and height measurements, while the main camera boasts expert precision for even more dimensional inspection.
Without multisensor metrology, the medical device industry has to rely on separate measuring tools for each dimensional characteristic. Because of the importance of precision, using multiple single-sensor systems makes for a lack of efficient inspection.
Automotive Multisensor Metrology
The automotive industry is known for repetition, large batches, and tight tolerances. Parts range in size but are manufactured in large batches. When these parts come out, they require dimensional measurement and GD&T information like position or flatness measurements.
Using a single-sensor machine for the automotive industry is not an incorrect choice, but multisensor systems take production efficiency to the next level. Combining multiple tools into one inspection solution reduces time, and allows for increased production.
Aerospace Multisensor Metrology
The aerospace industry manufactures complex, uniquely shaped parts, from enormous airplane wings to microscopic MEMS components. These parts undergo inspections throughout their lifespan for maximum safety, and the industry isn’t pushing out parts even close to as fast as automotive. The inspection process is lengthy, tedious, and precise to uphold the highest levels of safety for both spacecraft and aircraft.
A multisensor measurement system is a more efficient answer for the aerospace industry’s inspections. With a laser for easy plane measurements, camera for high precision dimensions, and a touch probe for some 3D shapes, the all-in-one multisensor system streamlines the inspection process and automates required AS9100 reporting.
Applications for Using Multisensor Measurement Systems
Because these systems are used in multiple industries, the applications are also diverse. Multisensor metrology excels at measuring and reverse engineering precision parts like stamped parts, fasteners, implants, and more.
Multisensor Measurement with Stamped Parts
A measurement focused multisensor measurement system utilizes a top down camera as it’s main sensor. This allows for easy profile measurements of stamped parts. Because stamped parts are usually flat, the camera is oftentimes the main sensor used, but occasionally the stamped parts will also be bent, which is where the probe comes in handy to measure an edge or an angle.
When the system gathers the image, technicians can physically see where angles and distances are. This probe and camera combination is helpful on parts with stamped height differences and bends.
Multisensor Measurement with Turned Parts
Turned parts are notably difficult to measure, with tricky dimensions like pitch diameter, thread angle, and runout. Having a multisensor measurement system with a rotary attachment allows for easy inspection of these dimensions on turned parts.
Multisensor Measurement with PCBs
PCBs are continuously getting smaller and smaller each year, making the inspection of these boards harder and harder to do with single sensor tools.
Multisensor measurement systems can effectively measure repetitive patterns, distances, heights and planes in just a couple seconds when combining the camera and laser sensors together. Also with mult-color illumination, these patters and platings are clearly visible for accurate inspection. These all-in-one tools speed up inspection, and are quickly becoming one of the only ways to fully inspect PCBs and keep up with demand.
Multisensor Measurement with Implants
Medical implants often benefit a patient’s life. However, if manufactured incorrectly, they can do more harm than good.
Implants have extremely tight tolerances for a correct fit and are sensitive to contact. Adding too much force, which could be a minimal amount, could ruin an implant's chance for beneficial use in a patient. This is why this type of metrology, with non-contact sensor options like vision and laser, is the best option for implants.
Multisensor Measurement with Reverse Engineering and Prototyping
A multisensor measurement system gathers entire dimensional information in one tool, simplifying the reverse engineering and prototyping process.
Additionally, the automation of multisensor systems allows for additional features like CAD integration. By connecting with CAD, it is easier to review and compare data with models. This helps optimize the precision and reliability of the entire process.
Adding Multisensor CMMs to Measurement Processes
Whether you manufacture for the medical device, aerospace, automotive, or other industry, a multisensor measurement system can work for you to streamline your processes.
At KEYENCE, we specialize in multisensor systems that use probes, cameras, lasers and light to take measurements. Our multisensor systems include additional features like statistical analysis, inspection reports, and on-screen visual guidance.
Contact us today to learn about our multisensor measurement system.
Related Downloads
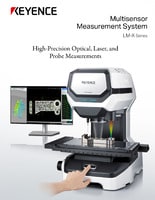
Brochure for the LM-X Series Multisensor Measurement System. Using optics, probes, and a multi-color laser to automatically measure all of your parts features.
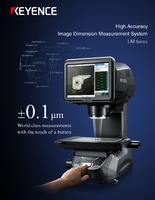
Brochure for the LM-1100 Series High Accuracy Image Dimension Measurement System. Submicron accuracy part inspection with non-contact height measurement.
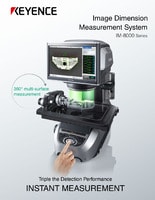
Brochure for the IM-8000 Series Image Dimension Measurement System. Accurately measure parts in seconds at the push of a button.