Laser Marking Systems / Laser Markers
3 Ways to Remove Oxidation From Aluminum
-
Tags:
- Metal , Laser Oxide Removal , Laser Cleaning
No manufacturer wants to see oxidized aluminum—it’s an unfortunate discoloration that signifies future corrosion. For example, if an aluminum sheet metal manufacturer has products that are exposed to a humid environment, oxidation or corrosion can be a costly issue. Oxygen in the air reacts with the aluminum, forming a thin layer of aluminum oxide on the exposed areas. This oxide layer is not visible to the naked eye but can weaken the surface and compromise the quality of the aluminum sheets.
Luckily, three aluminum oxidation removal processes are available for various applications and industries. This blog will review the basics of aluminum oxidation, what aluminum is, why it oxidizes more than other metals, why oxidation removal matters, and how to remove oxidation from aluminum.
What is Aluminum?
Aluminum is the most common metal on our planet and provides a great deal of functionality. It’s a soft metal that is easily malleable, can withstand heat, and is corrosion-resistant. Pure aluminum is not naturally occurring and wasn’t produced until 1824, but aluminum sulfates and compounds are found in many naturally occurring metals.
Because of its integration with metals, aluminum is found in various items: kitchen utensils, automotive components, gemstones, window frames, air conditioners, and so on. Considering the versatility, it’s likely that you’re in the presence of an aluminum item right now.
What is Aluminum Oxidation?
Aluminum oxidation is the beginning of aluminum’s corrosion process after bonding with oxygen. Oxidation occurs to protect the aluminum from corroding further. It may appear as a discoloration or as an off-white color.
Removing Oxide with Laser Markers
Why Remove Aluminum Oxidation?
The two main reasons for removing aluminum oxidation are aesthetics and further corrosion prevention.
As mentioned above, aluminum oxidation creates discoloration or an off-white color. This coloring may be unappealing to look at because it appears dirty.
For the practical side of removing aluminum oxidation, conducting frequent cleanings prevents your aluminum from oxidizing or corroding further. The longer that the aluminum oxidizes, the more difficult it will be to remove. The aluminum oxidation will eventually make the aluminum product perform poorly.
How to Remove Oxidation from Aluminum - 3 Methods
- 1. Chemical Sprays or Soaks
- Chemical sprays or soaks are sold at retailers like Amazon, Walmart, or Target and are used for intense oxide removals, such as on automobiles or boats. These sprays are made of hydrofluoric acid, sulfuric acid, and phosphoric acid, which requires more protective gear than DIY methods.
Spray or soak the infected area with the chemicals, scrub, and rinse. Then repeat accordingly. The brand, chemicals, and intensity of aluminum oxidation will determine how long this process takes and specific instructions.
Using chemical sprays or soaks is preferable in low volume settings, especially if the part is an aluminum alloy. These chemicals do not have a reaction with the other metals in the alloy and leave behind a clean finish. For instance, the aerospace industry can benefit from these soaks because of the frequent copper, zinc, and magnesium alloys with aluminum. Additionally, it doesn’t risk creating accidental holes, cavities, or deformities that may affect the functionality of the part, which is possible with sanding. - 2. Laser Ablation
- Laser ablation, also known as laser cleaning, is an automated method for removing aluminum oxidation. Ablation works by using a powerful laser beam with short pulse frequencies to heat the oxidation to the point of evaporation.
There are different types of lasers used for laser ablation. However, at KEYENCE, we recommend a fiber laser or a hybrid laser because of the power capabilities. Using a laser is an automated process, instead of the manual methods. There isn’t any scrubbing, soaking, or rinsing involved. Instead, the removal process takes a few seconds and is completed in one step.
Laser ablation is ideal for manufacturing operations, and excels with parts smaller than 30cm x 30cm. Laser ablation is unique in that it can target precise areas of oxidation even in hard-to-reach spots of non geometric shaped parts. Medical devices benefit from laser ablation because of the corners and curves that may harvest oxidation. - 3. Fine Grit Sandpaper
- Fine-grit sandpaper is an effective way to remove oxidation without chemicals or heat. It requires a few steps of cleaning pre and post-sanding. The oxidized aluminum can be sanded off with a sanding machine or by manually sanding the part.
First, use a microfiber towel to get the oxidized aluminum area as clean as possible. Once the area is as clean as possible with the microfiber towel, the area must be washed with soap and water.
Pressurized hoses help make the surface as clean as possible. When the area reaches satisfactory cleanliness, it must be dried again with a microfiber cloth. Now, the surface can be sanded. Starting with 240-320 grit sandpaper, smooth the surface and work your way up to fine grit sandpaper of 800-1,000 grit. Once the aluminum oxidation is removed, use a microfiber cloth to remove the dust and spray it down with a hose. Dry with microfiber and add anti-corrosion polish.
This method is ideal for medium-sized surface areas, like the rim of automotive wheels. However, it may not be best for very small or big areas because of how tedious it is.
Looking to Use Laser Ablation?
At KEYENCE, we specialize in laser ablation with our laser marking machines. The laser markers include features like autofocus, 3-axis control, and integration of CAD data to make the aluminum oxidation removal process quick and easy on any target. From tiny metal tools to large automotive parts, the strength and positioning skills of the hybrid and fiber laser tackle anything.
Ready to see laser aluminum oxide removal in person? Contact KEYENCE to request a demo or discuss any questions!
Related Downloads
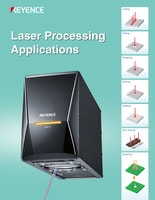
This booklet covers a wide range of laser processing techniques - such as cutting, drilling, and deep engraving - as well as welding and soldering that are unique to lasers.