Data Acquisition (DAQ)
What is CAN? (Controller Area Network)
CAN is an acronym for Controller Area Network and represents a robust vehicle bus standard designed to allow microcontrollers and devices to communicate within a vehicle without needing a host computer. This particular bus was developed by Bosch for automotive applications to reduce the complexities and wiring in vehicles.
This section explains the “CAN,” a communication protocol used not only for automobiles but also for other factory automation industrial equipment.
History of CAN
The controller area network (CAN) is a serial communication protocol developed by the German company Bosch. The word CAN may remind many people of automobiles. This protocol was completed in 1985 and was first adopted in mass-produced cars in 1990. Then, in 1994, the International Organization for Standardization (ISO) standardized it as ISO 11898 and ISO 11519. Today, the protocol is adopted on almost all automobiles. Furthermore, CAN is being utilized in a wide variety of fields, including factory automation (FA).
We’re here to provide you with more details.
Reach out today!
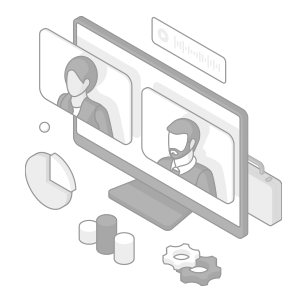
Necessity of CAN
CAN was originally developed to be utilized within automobiles, but now this technology is utilized at factories, as well as on medical and other worksites. The background behind this technology was the necessity to support an increasing number of electronic control units (ECUs) in parallel with the performance enhancement of automobiles. More complicated control means more I/Os and larger ECUs, and data sharing among multiple ECUs also increases the number of wires. These factors will lead to complicated, heavier automobiles with more components, which will require much higher production costs. A solution for this situation was a CAN serial communication protocol that enables high-speed and reliable communication with a small number of wires.
Conventional Communication Method
- A large number of wires.
- More weight.
- Need to secure enough wiring space.
- An increased number of physical wires increases the risk of faults.
- Fault diagnosis requires each ECU to be inspected separately.
CAN-Based Communication Method
- Connection is possible with a small number of harnesses.
- Easy communication between ECUs.
- High scalability.
- One piece of information can be shared between multiple ECUs.
- Fault diagnosis and processing for the entire network can be done at a single location.
Curious about our pricing?
Click here to find out more.
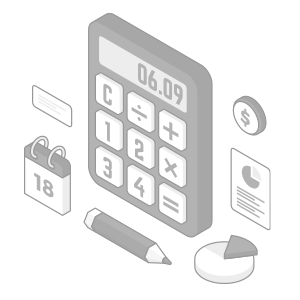
Types of Communication Protocols
In addition to CAN, other communication protocols−including the LIN, the FlexRay, and the MOST−are also used in on-board networks. The LIN, which is intended to be used as a CAN subnetwork, is a standard that enables serial communication at a low cost. On the other hand, the FlexRay, which has received attention as a next-generation on-board network, enables faster communication than CAN. While CAN, the LIN, and the FlexRay are mainly used for communication to control engines, the Media Oriented Systems Transport (MOST) is intended for multi-media system communication. As outlined here, there are various communication protocols in addition to CAN.
Communication protocol | Maximum communication speed |
---|---|
Communication protocol
CAN
|
Maximum communication speed
1 Mbps
|
Communication protocol
LIN
|
Maximum communication speed
20 kbps
|
Communication protocol
FlexRay
|
Maximum communication speed
10 Mbps
|
Communication protocol
MOST
|
Maximum communication speed
24.8 Mbps
(standards for 50 Mbps and 150 Mbps also exist) |
As shown above, each protocol offers different communication speeds. However, the faster the communication protocol, the higher the cost, so you need to select an appropriate one according to your requirements.
Discover more about this product.
Click here to book your demo.
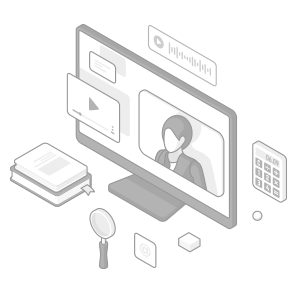
Types of CAN
CAN is classified according to the communication speed into the high-speed CAN “CAN-C,” the low-speed CAN “CAN-B,” etc. Furthermore, the Society of Automotive Engineers (SAE) classifies CAN based on the communication speed as follows.
Class | Communication speed | Applications |
---|---|---|
Class
Class A
|
Communication speed
Up to 10 kbps
|
Applications
Lights, power windows, door locks, etc.
|
Class
Class B
|
Communication speed
10 to 125 kbps
|
Applications
Meters and other status information systems such as those for automatic air conditioners and fault diagnosis.
|
Class
Class C
|
Communication speed
125 kbps to 1 Mbps
|
Applications
Real-time control systems for engines, transmissions, brakes, etc.
|
We’re here to provide you with more details.
Reach out today!
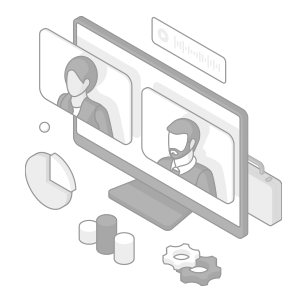
Importance of CAN Protocol
The importance of CAN protocol lies in its reliability, robustness, simplicity, and effectiveness as a communication protocol between various electronic control units within a vehicle. This reduces the complexity and weight of wiring, improving vehicle performance and enhancing the diagnostic capabilities of the vehicle.
However, CAN protocol is used in industrial settings as well for performing different measurements. For example, KEYENCE’s NR-X Series multi-input data logger or NR-500 multi-input DAQ can process CAN data measurements, which is crucial for vehicle testing, performance analysis, and research and development.
Get detailed information on our products by downloading our catalog.
View Catalog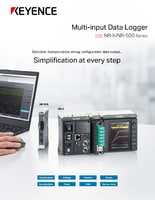
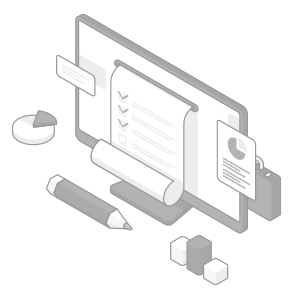
Implementation of CAN Communication Protocol
Implementing the CAN communication protocol involves setting up a network of ECUs and sensors connected through a two-wire bus. Each node in the network sends and receives messages based on identifiers that determine message priority. CAN protocols ensure that the highest priority message is transmitted first.
Discover more about this product.
Click here to book your demo.
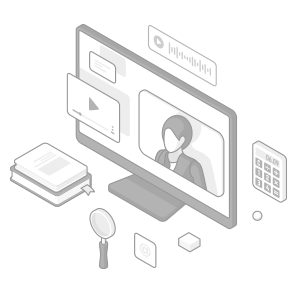
Types of CAN Messages
CAN protocol is a message-based protocol that relies on several different types of messages:
- Data Frame: Carries data from the transmitter to the receivers.
- Remote Frame: Requests data from another device.
- Error Frame: Transmitted by any node that detects an error.
- Overload Frame: This indicates that a node is too busy to process further requests.
Advantages of CAN Bus
As stated above, Bosch designed the CAN bus protocol to reduce the wiring inside the vehicle, especially compared to traditional wiring in older vehicles. This is a rather robust system that provides real-time readings and communication complemented with priority-based message arbitration and error messaging and signaling capabilities. The CAN bus is rather flexible, and you can easily add new devices to the network without having to make major changes to the existing system.
We’re here to provide you with more details.
Reach out today!
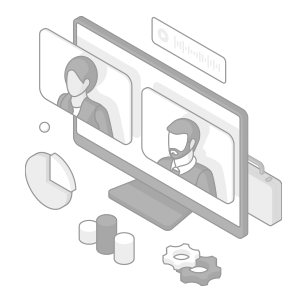
What is the CAN FD?
FD stands for “Flexible Data RATE,” which is the extension of the original CAN protocol. It supports higher data rate and larger data payloads per frame. These enhancements allow more efficient data transmission, which is convenient considering the increasingly complex and data-intensive systems equipped in modern vehicles.
Discover more about this product.
Click here to book your demo.
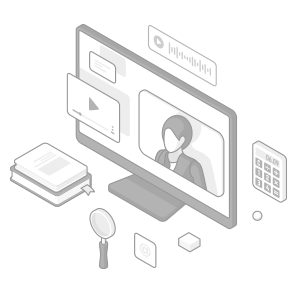
FAQs about CAN Protocol
What CAN Protocol Is Used in Automotive?
The modern automotive industry relies on CAN 2.0A and 2.0B protocols, as well as on CAN FD, depending on the application’s requirements for data transmission speed and the volume of transmitted data.
Is CAN a Communication Protocol?
Yes, CAN is a communications protocol specifically designed to provide more efficient communication between electronic devices inside the vehicle without the need for a central processing unit or a central computer.
Why Is CAN So Important?
CAN protocol is important because it reduces vehicle wiring and enhances reliability and diagnostic capabilities while also providing real-time communications with high-fault tolerance, which is crucial in both automotive and industrial environments—data loggers can record and transmit data over the CAN bus.
What Is The Difference Between CAN and LIN?
CAN and LIN (Local Interconnect Network) are both communication protocols used in vehicles but serve different purposes. CAN is used for high-speed communications and critical systems, while LIN is simpler, slower, and used for non-critical control applications like windows, mirrors, and seats. LIN networks are often used as subnetworks within larger CAN networks due to their cost-effectiveness for simple control tasks.
Interested in enhancing your vehicle's diagnostic capabilities with real-time communication and high-fault tolerance? Check out KEYENCE’s data loggers for CAN data measurement applications.
Contact us today to see how we can help your business operations!